油液集中供液系统工程机械论文
“月が綺麗”通过精心收集,向本站投稿了14篇油液集中供液系统工程机械论文,下面是小编精心整理后的油液集中供液系统工程机械论文,希望能够帮助到大家。
篇1:油液集中供液系统工程机械论文
油液集中供液系统工程机械论文
1集中供液系统的输送介质
(1)柴油。
(2)液压油。
(3)防冻液。
(4)冷媒。
(5)其他如柴机油(加注在发动机及变速箱中)、齿轮油(加注在后桥,蜗轮箱等传动机构中)。工程机械行业中由于柴油及液压油使用量加大,其余油液使用量较小,故柴油及液压油多使用集中供液系统,而其余油品则使用线边加注机加注的模式。
2集中供液系统的构成及简介
2.1储液系统
主要由进液系统、储液罐、供液系统、泵房等组成。
(1)进液系统。为满足油罐车输送方式,多在墙体上布置柴油、液压油油罐车卸油快速接头。柴油油罐车一般自带卸油泵,故柴油不配卸油泵;液压油配卸油泵,同时满足油桶补油方式和油罐车不带泵时的补液方式,同时液压油卸油配置防空打保护装置,桶空时能自动关闭卸油泵。考虑到要快速吸纳液体的需要,即流量为主要因素时,采用气动隔膜泵,GRACO:H2150型气动隔膜泵,见图2。对于输送有腐蚀性的液体时,应采用不锈钢的泵和管路,如防冻液、冷媒等液体。另外,在进液泵的前端应设置过滤器,除去液体中的部分杂质。
(2)储液罐。根据每车加注量、生产纲领和加注频率的需要,计算出需要的储液罐数量和罐体规格。同时,还要考虑输送液体的性质,如有腐蚀性,应采用不锈钢罐体,如防冻液、冷媒等液体。其他无腐蚀性液体,可采用一般的碳钢罐体。储液罐卧式放置,推荐采用埋地方式,外表面做五油三布加强级防腐处理。储液罐通气管管口上装阻火透气帽,在呼吸阻火阀处要加装干燥器,避免潮湿的空气进入油罐造成油液乳化。每个储液罐均安装有液位控制传感器,高、低液位及极限液位时自动报警。
(3)供液系统。根据输送液体的粘度和输送距离,柴油选用气动隔膜泵。液压油粘度较大,输送泵选用大流量气动柱塞泵。油液输送泵每种油品均配备双泵,一用一备,正常使用一台,留有一个泵作为系统备份。输送系统分别配置过滤器及流量计,用于物料统计。流量计一般安装在储液罐的出油口处,可以避免由于罐车卸油或油桶补油时出现空打,造成流量计计量不准的情况发生。
(4)泵房。因柴油属于“乙类”易燃液体,为确保安全,泵房内照明、排气线路及开关均采用防爆装置,同时用自动防爆排风扇强制换气方式减少泵房内挥发可燃气的存在。同时,油泵房内设有可燃气体检测报警器,当可燃气体达到爆炸下限浓度(V%)值时报警。泵房所有的气动马达都要接地线至泵房的总地线上,将运动件摩擦和流体运动产生的静电放掉。地面设集油槽,方便废液回收。
2.2输送管路系统
输油管路、控制信号管路分别实现油液的输送及控制信号的传递,一般车间外埋地铺设,车间内加空铺设,并采用五油三布加强级防腐处理。输油管路一般是长度在6~8米不等的无缝钢管采用“单面焊接,双面成型”方式连接而成,不同油液的管路标有不同颜色,并用文字标识,以便与区分。在输送泵出口设计压力传感器,当用油点没有使用油品而输送管路里的油品压力有明显压降现象,此时集中供液监控系统应及时报警,提示工作人员及时检测输送管是否有漏油情况。当夏季或发生火灾时,管道内的油液因为温升较高导致体积迅速膨胀,从而使管道内瞬间产生更高的压力时,压力传感器检测到压力超过设定值时会进行报警,并开启旁通安全阀进行泄压。集中供液的储液罐及各泵、管路安装完毕,同时进行压力检漏。检漏合格后进行压缩空气清扫,清扫完毕后用相应的油液进行清洗。
2.3加注系统
一般在加注工位设置需要的'加注机,一些工程机械油液加注口位于机器上部,还配有可伸缩加注平台,如柴油加注机、液压油加注机、防冻液加注机及其他油品加注机。液压油二合一加注机(带伸缩平台)液压油二合一加注机(带伸缩平台)主体由两配置相同的液压油管路组成,补液管路采用集中供液的补液形式,储液箱配置液位传感器,可实现自动补液及错误报警功能,加注泵采用JUSTMARK齿轮泵,加注管路配置溢流阀保证管路安全,加注管路配置美国Donaldson过滤器,确保油品质量;可伸缩平台实现不同车型车辆的加注。加注流程:首先选择需要的加注车型,然后将对应加注枪与工件的加注口连接。打开加注枪扳机,按下对应加注启动按钮,进入加注过程。加注完成后,加注指示灯灭,蜂鸣提示,最后取下对应加注枪,将加注枪放回加注枪架位置。除加注和撤卸加注枪采用人工方式外,其他所有加注过程都是自动完成。
2.4电气控制系统
电气控制系统采用PLC和触摸屏的方式,主要用于对输送泵的远程输送进行控制,主要包括液压油补液启停、输送泵的控制、储液罐液位传感器的控制及不同油液加注量的统计。主控柜显示面板上显示供液管路的工作状态及报警信息,可以分别进入不同的窗口以全面了解系统的各项指标和工作状态。液位高度上设定4个点,分别为液位上限、上限保护、液位下限和下限保护,当液位到达液位下限时,报警提示补液(此时应预留一定的量,以免影响生产);当油液到达液位上限时,报警提示油液已满,补液泵自动停止,上限保护是防止液位上限失效后,补液时油液溢出。下限保护,是当液位到达下限保护液位时,停止输送泵工作,防止输送泵空打。为保证系统安全可靠的运行,加注端与油库集中控制柜信号互锁,当线边加注设备需要油液时,先打开加注设备内的阀,并延时5秒后启动输送泵,当线边加注设备不需要油液时,控制输送泵停止,延时5秒后关闭加注设备内的阀,管路内始终处于零压力状态,防止管路出现泄漏事故。通过储液罐出口的流量计,系统能够按时间节点(年、月、周、日)将输送油品量信息进行统计,计量每种油品输送到加注机的总量,为降低消耗、实现安全生产提供可靠的理论依据。
篇2:工程机械液压系统论文
工程机械液压系统论文怎么写,该专业的同学都知道,液压系统是当前机械使用中的主要体系,是通过液压系统促进机械运行的方式,我们看看下面的相关论文吧!
工程机械液压系统论文
【摘 要】随着当前建筑行业发展中,越来越多的建筑施工机械应用在建筑施工之中,成为当前建筑施工的主要的施工体系。工程机械液压系统是当前工程机械使用的主要系统,其在使用的过程中能够有效的提高施工效率和提高施工质量。然而其在施工的过程中容易受到各种外在因素的影响而造成施工的干扰。本文分析了在工程机械液压系统使用中的各种影响因素和危害,并提出其相应的维护措施和管理手段。
【关键词】工程机械;液压系统;维护
在当前社会发展中,液压系统是当前施工机械应用的主要形式,其正常运行与否是当前液压技术的衡量标准和判断依据。合格的液压油是液压系统可靠运行的保障,在液压系统使用的过程中合格的液压系统是其正常可靠运行的关键,更是提高施工质量和施工效率的主要方法和措施。
1 选择适合的液压油
液压油是当前液压系统中的重要组成成分,其在液压系统中起着重大的作用,主要作用表现在传递压力、润滑、冷却、密封,液压油的选择是不可忽视的过程,其在选择的过程中良好的液压油不但能够保证液压系统的正常有序运行,更能够提高运行速度,增加运行的效率和保障机械使用寿命。液压油选择不恰当是液压系统早期故障和耐久性下降的主要原因。因此在建筑施工机械工作的过程中,对液压油要选择能够与本机型相搭配的,避免由于也要有选择的不是引起的施工故障和施工缺陷,由于特殊情况的影响需要使用代用油的时候,要结合其品牌和性能进行选择。不能够使得其进行混合使用。避免由于液压油发生化学反应而造成的影响损失。
2 防止固体杂质混入液压系统
清洁的液压油是液压系统的生命。 液压系统中有许多精密偶件,有的有阻尼小孔、有的有缝隙等。若固体杂质入侵将造成精密偶件拉伤、发卡、油道堵塞等,危及液压系统的安全运行。一般固体杂质入侵液压系统的途径有:液压油不洁;加油工具不洁;加油和维修、保养不慎;液压元件脱屑等。可以从以下几个方面防止固体杂质入侵系统:
2.1加油时
液压油必须过滤加注,加油工具应可靠清洁。不能为了提高加油速度而去掉油箱加油口处的过滤器。加油人员应使用干净的手套和工作服,以防固体杂质和纤维杂质掉入油中。
2.2保养时
拆卸液压油箱加油盖、滤清器盖、检测孔、液压油管等部位,造成系统油道暴露时要避开扬尘,拆卸部位要先彻底清洁后才能打开。如拆卸液压油箱加油盖时,先除去油箱盖四周的泥土,拧松油箱盖后,清除残留在接合部位的杂物(不能用水冲洗以免水渗入油箱),确认清洁后才能打开油箱盖。如需使用擦拭材料和铁锤时,应选择不掉纤维杂质的擦拭材料和击打面附着橡胶的专用铁锤。
2.3液压系统的清洗
液压系统由于在长期工作的过程中使用液压油和其他因素造成的油垢,这些油垢随着长期的积累逐步的沉积下来,形成影响液压系统正常运行的主要因素,因此在其使用的过程中要通过清晰方式除去其中油垢。清洗油必须使用与系统所用牌号相同的液压油,油温在45~80℃之间,用大流量尽可能将系统中杂质带走。液压系统要反复清洗三次以上,每次清洗完后,趁油热时将其全部放出系统。清洗完毕再清洗滤清器、更换新滤芯后加注新油。
3作业中注意事项
3.1机械作业要柔和平顺
机械作业应避免粗暴,否则必然产生冲击负荷,使机械故障频发,大大缩短使用寿命。作业时产生的冲击负荷,一方面使机械结构件早期磨损、断裂、破碎,一方面使液压系统中产生冲击压力,冲击压力又会使液压元件损坏、油封和高压油管接头与胶管的压合处过早失效漏油或爆管、溢流阀频繁动作油温上升。还有一个值得注意的问题 :操作手要保持稳定。因为每台设备操纵系统的自由间隙都有一定差异,连接部位的磨损程度不同因而其间隙也不同,发动机及液压系统出力的大小也不尽相同,这些因素赋予了设备的个性。只有使用该设备的操作手认真摸索,修正自己的操纵动作以适应设备的个性,经过长期作业后,才能养成符合设备个性的良好操作习惯。一般机械行业坚持定人定机制度,这也是因素之一。
3.2要注意气蚀和溢流噪声
作业中要时刻注意液压泵和溢流阀的声音,如果液压泵出现“气蚀”噪声,经排气后不能消除,应查明原因排除故障后才能使用。如果某执行元件在没有负荷时动作缓慢,并伴有溢流阀溢流声响,应立即停机检修。
3.3严格执行交接班制度
交班司机停放机械时,要保证接班司机检查时的安全和检查到准确的油位。系统是否渗漏、连接是否松动、活塞杆和液压胶管是否撞伤、液压泵的低压进油管连接是否可靠、油箱油位是否正确等,是接班司机对液压系统检查的重点。
3.4保持适宜的油温
液压系统的工作温度一般控制在30~80℃之间为宜(危险温度≥100℃)。液压系统的油温过高会导致:油的粘度降低,容易引起泄漏,效率下降;润滑油膜强度降低,加速机械的磨损;生成碳化物和淤碴;油液氧化加速油质恶化;油封、高压胶管过早老化等。
为了避免温度过高:不要长期过载;注意散热器散热片不要被油污染,以防尘土附着影响散热效果;保持足够的油量以利于油的循环散热;炎热的夏季不要全天作业,要避开中午高温时间。油温过低时,油的粘度大,流动性差,阻力大,工作效率低;当油温低于20℃时,急转弯易损坏液压马达、阀、管道等。此时需要进行暖机运转,起动发动机,空载怠速运转3~5min后,以中速油门提高发动机转速,操纵手柄使工作装置的任何一个动作(如挖掘机张斗)至极限位置,保持3~5min使液压油通过溢流升温。如果油温更低则需要适当增加暖机运转时间。
3.6液压油箱气压和油量的控制
压力式油箱在工作中要随时注意油箱气压,其压力必须保持在随机《使用说明书》规定的范围内。压力过低,油泵吸油不足易损坏,压力过高,会使液压系统漏油,容易造成低压油路爆管。对维修和换油后的设备,排尽系统中的空气后,要按随机《使用说明书》规定的检查油位状态,将机器停在平整的地方,发动机熄火15min后重新检查油位,必要时予以补充。
3.6其他注意事项
作业中要防止飞落石块打击液压油缸、活塞杆、液压油管等部件。活塞杆上如果有小点击伤,要及时用油石将小点周围棱边磨去,以防破坏活塞杆的密封装置,在不漏油的情况下可继续使用。
4 定期保养注意事项
目前有的工程机械液压系统设置了智能装置,该装置对液压系统某些隐患有警示功能,但其监测范围和程度有一定的局限性,所以液压系统的检查保养应将智能装置监测结果与定期检查保养相结合。
5 小结
保养与维护制度是液压系统使用中的主要方式,是利用相关的技术手段进行管理和控制的过程。做好维护保养措施能够有效的提高工程机械施工效率和施工质量,提高工程施工效益。
[工程机械液压系统论文]
篇3:电控系统工程机械论文
电控系统工程机械论文
1Parker电控系统硬件系统
1.1控制器
Parker具有多种控制器,包括支持CAN协议、多线程、带大型液晶显示、带触控屏、支持安全功能等多款主控制器及扩展控制器。Parker的控制器根据开发平台的不同分为三种系列,首先是基于Matlab/Simulink编程的CM系列,主要用于大批量定制化的控制系统,如用于控制变速箱的CM0711,用于控制挖掘机、装载机的CM3620等;其次是基于模块化编程平台的IQAN系列,主要用于中小批量且用户可编程的控制系统,如用于控制比例阀的XA2、用于控制高空作业设备的安全模块MC3等;还有基于梯形图编程形式的VMM系列,主要用于多路复用控制系统,如用于控制风扇散热系统的VMM0604等。Parker的控制器采用坚固的壳体设计,配备车载防护连接器,内部具有防止冷凝隔膜,具有高可靠性及耐用性,严格符合国际标准,适用于室外环境使用。
1.2显示器
Parker的显示器包括支持CANJ1939协议、ISOBUS协议、配置大型液晶屏、触控屏、多仪表板等多种类型。多年以来的应用,证明了产品的技术及稳定性完全符合各种工况需求。例如运用了完全集成型高亮度的IQAN-MD4显示器,可在IQANdesign环境中快速进行配置,用户可编程的全新触摸显示屏为工业车辆提供了直观的界面。MD4显示器分为5.5英寸、7英寸和10英寸三种型号,支持摄像头视频信号输入与显示,使驾驶操作更加简便智能。
1.3传感器
Parker具有广泛的传感器系列,包括压力、温度、接近,速度、转角及倾角等。产品的先进技术及稳定性完全符合各种工况需求,经过不断研发创新,设备精度在同类产品中处于领先水平。
1.4手柄等附件
Parker的手柄设计紧凑、质量轻、安装尺寸小、操作力小,具有耐候性和安全性等特点,特别适用于精确控制。手柄通过CAN总线与其他模块连接,大量的输入接口使基座成为很好的输入模块。Parker的.手柄主要有LC5系列、LC6系列、LSL系列和LST系列。LC5系列是大型多轴向手柄,任意方向的全行程力达到100Nm,具备较大的抗扭强度,适用于户外使用。LC5手柄内部采用非接触霍尔型双路传感器,为高安全性和可靠性提供保证。此外,手柄的基座、壳体、波纹套、按键数量、滚轮数量、触发开关等都可以根据用户需求进行定制,以满足用户的不同控制要求。LC6系列手柄作为LC5系列的升级版,增加了手柄自由度,从而增加了模拟量输入接口,减少了复杂系统操控时的手柄复用。同时其安装更加简化,具有更强的抗噪能力和更长的使用寿命。LSL系列是单轴手柄,有中位止动、手柄顶部开关、电磁止动几种选配,用于液压比例控制。LST系列是一款微型手柄,安装在工程机械的座椅扶手或仪表板上,用于液压比例控制。此外,Parker还有电子油门踏板、USB-DLA数据服务工具、诊断和网关模块、线束接插件等产品,以供用户进行选配。
1.5应用案例
为基于Parker控制器的挖掘机电控系统硬件解决方案。该方案的核心控制器是CM3620主模块,它拥有36个输入和20个输出,具有2路CAN/J1939接口和1路RS232通信接口,可满足用户的控制需求。该系统还使用了显示器和G1诊断网关,同时配备了与上位机软件进行交互的DLA数据服务工具。使用的传感器主要有电子油门旋钮、压力传感器、温度传感器、速度传感器、液位传感器等。
2软件开发平台
Parker电控系统基于IQAN、VMM、Raptor三种开发平台。IQAN平台是基于模块化编程的开发平台,用户无需具备编程经验,可以直接设计所期望的机器功能。它包含了IQAN-design、IQAN-Simulate、IQAN-run等软件。IQAN-design是高级的图形设计工具,它简化了行走机械应用程序的开发,从而缩短了开发时间。该工具提供了大量的预定义模块,如闭环控制,信号处理,数学计算,通讯协议和系统诊断等,主要用于系统布局和机器功能设计。IQAN-simulate是仿真工具,能够仿真IQAN应用程序中的所有硬件模块,在应用程序中可方便地使用屏幕上的拖动条对所有输入量进行仿真。在仿真输入的同时可以测量结果(输出值),也可以进行FEMA(失效模式分析)。软件仿真比在实际机器上测试新应用程序更安全。仿真运行和实际状态一样,可以查看显示界面,调整参数,观察记录,测试用户界面等内容。IQAN-run可以在开发阶段运用“高级图形测量”和“机器统计数据收集”功能优化机器性能。IQAN-analyze是通用的CAN总线分析仪。用户可以通过简便的方式观察CAN总线上的通讯,也可以记录所观察的数据并进行保存供日后使用。是基于梯形图编程的软件开发平台。该平台采用多路复用技术,将控制模块通过J1939屏蔽双绞线互联,允许模块可以接收输入、驱动输出,并将输入输出信息通信给系统中的其他部件。梯形逻辑中的输入和输出可以来自通过J1939网络连接到一起的一个或多个模块。Raptor平台是基于Matlab/simulink编程的开发平台。该平台是CAN协议图形化定义工具,拥有图形化的应用程序界面,而且具有Motohawk到Raptor的自动转化脚本。为基于IQAN平台开发的小型液压挖掘机电控系统。根据硬件选型结果拖拽到编译系统中进行逻辑连接,对各模块进行参数设置,并对主模块进行编程。主程序包括“Joysticks”、“Engine”、“Diagnostics”、“Blade”、“Excavator”六个功能组,通过对输入输出的设置以及内部通道的逻辑和算法,实现对整机性能的精确控制。
3系统仿真
系统仿真主要通过IQAN软件自带的“IQAN-Run”和“IQAN-Simulate”进行。IQAN-Run用来对程序进行运行和调试,主要包括调参数、设置比较、设置权限、上传/下载程序以及日志管理等功能;IQAN-Simulate用来对应用程序进行虚拟仿真,以及系统的演示和验证。所示为小型液压挖掘机电控系统的仿真。将编写好的小挖程序进行参数设置,并手动调节手柄的模拟量输入,可以得到显示模块中相应参数值的变化。还可将其中的参数值设为可调恒。
4总结
Parker产品具有多种硬件序列,提高了硬件选型的灵活性,针对不同机型的应用可选择更加合适的硬件系统;Parker的三种软件开发平台,突显了可视化编程的便捷性与直观性。基于Parker控制器的工程机械电控系统满足了可靠性、舒适性以及操控灵活性的要求,并以其较高的性价比兼顾了工程机械的成本限制因素;同时,该电控系统设计符合控制系统开发“V字形”流程,精简了开发环节,减少了检测和调试次数,节约了时间和成本。
篇4:液压系统工程机械论文
1.工程液压系统维护
1.1定期对液压系统进行保养
对现在使用的各种工程机械进行调查发现,现在的工程机械的液压系统基本上都安装了智能设备,可以对液压系统故障进行警示,但作用范围有限。所以,在液压系统的检查保养过程中,应该讲定期检查和智能设备监测结合起来。第一,250小时检查保养。定期对滤清器滤网进行检查,如果滤网中金属粉末有些多,则说明油泵有磨损。此时需进行确诊,采取有效的措施后方可开机。第二,500小时检查保养。当工程液压系统运行累计500小时以后,不管滤芯实际处于何种状态都要对其进行更换。第三,1000小时检查保养。要对液压油箱、滤清器进行彻底清洗,并且液压油进行更换,如果系统长期工作在高温条件下,则应当提前换油。第四,7000小时、10000小时检查维护。此时要由专门的工程液压系统检测人员对系统进行检测,根据实际情况进行适当的调整、维修。
1.2防止杂质、空气以及水等进入液压系统
从某种意义上来讲,液压油自身是否清洁,在很大程度上关系着整个液压系统的服役期限和运行效率。从液压系统运行实践来看,该系统中有多个精密偶件构成,尤其是阻尼小孔比较多,一旦有固体杂质等进入其中,那么必然会导致精密偶件遭受一定的拉伤,甚至会阻塞油道,更为严重时会导致液压系统无法正常运行。同时,还要防止空气、水等侵入液压系统。第一,常温常压条件下,液压油中大约含有7%的空气,随着压力的不断降低,空气从油中逐渐游离出来,当气泡破裂时,液压元件会出现“气蚀”现象,而且还会产生较大的噪声。当空气进入油液后,就会造成气蚀现象加剧,与此同时液压油的压缩性也会不断地变化(通常是不断的增大),并且表现出一定的不稳定性,严重影响液压系统运行效率。第二,一旦液压油中的含水量超标,则可能会造成液压元件大量锈蚀,严重时可能会导致油液乳化变质,甚至会导致机械设备严重磨损。在液压系统维修和保养过程中,应当确保水分不进入到油液之中,同时还要将储油桶盖拧紧,必要时需对其进行倒置,以免水分进行其中。
1.3液压油合理选择
液压油对于工程液压系统而言非常重要,其作用体现在润滑、压力传递、密封和冷却等方面,通常工程机械液压系统故障和耐久性降低的主要成因就是液压油选择不当。对于这一问题,应当严格按照使用说明书中要求的牌号选用正确的液压油,对于有特殊要求的,要特别注意使用液压油性能和原牌号要求性能之间的一致性。
2.结语
总而言之,工程液压系统故障问题较为常见,而且故障成因多样化,为确保液压系统的正常运行,需根据实际情况做好诊断工作。同时,还要注意故障防范,即做好日常要维修和养护工作。笔者认为,将事前故障问题防范与故障诊断工作结合起来,才能确保液压系统正常运行。
篇5:液压系统工程机械论文
1.工程机械液压系统泄露的危害
在机械液压系统中,液压油是非常重要的。因为液压油既是机械液压系统中传递动力的介质,又对液压元件起着润滑作用。所以,液压油的泄露会给液压系统造成很多危害,主要危害如下:
1.1对机器性能的影响
机械液压系统中液压油的泄漏,必然会造成压力的损失,从而导致液压系统工作速度及力度等等的减弱,从而会影响机器本身的工作性能。其次,泄漏也会使外界污物容易入侵液压系统,造成恶性循环,使主机或元件磨损,影响设备使用。
1.2造成施工对象的损失
机械液压系统中液压油的泄漏会污染环境,而且有时候会影响工程质量,严重者甚至造成返工。比如:铺设高等级沥青路面是不允许有油污的。如果在施工过程中,压路机或摊铺机泄漏了液压油,那么必须将有油污的路段铲除,重新铺设。这样就会造成大量的原材料、人力和时间的浪费。
1.3损失液压油
工程机械液压系统所使用的液压油,一般是比较贵的,其价格与食用油差不多。如果造成损失,将是极大的'浪费。
1.4系统发热
一般液压系统泄漏都会伴随动力不足和系统发热。系统发热容易将系统变成超高温热源,容易引起火灾。
2.工程机械液压系统泄露的主要部位
2.1管接头
管接头的泄漏主要因素有:紧固强度、连接处的加工精度及毛刺是否清除干净等。主要原因是:螺栓蠕变松动,管接头的类型与使用条件不符,压力脉动引起接头松动,管接头设计结构不合理,接头拧紧力过大或不够、不均匀,接头加工质量差不起密封作用。
2.2元件接合面
在元器件的结合面发生泄漏主要原因有:密封表面粗糙度误差过大;密封设计不符合规范要求;密封配合精度低、配合间隙超差;密封结构选用不当,造成变形,使接合面不能全面接触;密封沟槽的尺寸不合理;装配不细心,结合面有沙尘或野蛮装配造成损伤,产生较大的塑性变形。
2.3密封件
密封件造成液压系统泄漏主要是由于密封件损坏或密封作用降低,主要原因有:密封件的几何精度不合格、密封件的材料或结构类型与使用条件不相符、加工质量低劣、密封件安装错位、密封件失效、表面磨损、密封件压缩量不够、密封件的技术指标不合要求、密封垫硬化或热处理不当、密封件寿命到期未及时更换、密封件老化损伤。
2.4壳体
液压系统壳体的泄漏主要发生在焊接件和铸件上,它是由于焊接和铸造时产生的缺陷在液压系统的冲击振动或压力脉动作用下逐渐扩大而引起的。
3.泄露的原因
造成机械液压系统泄露的原因有很多,不管是从方案设计到工艺过程;还是从密封件的质量到维护管理等等都有可能造成泄露。机械液压系统泄露的原因复杂多样,主要是:系统的设计、元件的生产制造、系统管路的连接安装、系统的装配、系统使用及维护等等因素有关。总之,液压系统泄露的主要原因是来自间隙控制问题、液压冲击问题和温升发热问题。间隙控制问题是指元器件与容腔间的间隙不适现象。主要表现为:
(1)原始间隙不妥,主要是设计或加工不合理;
(2)装配引起的间隙畸变,主要是装配过程中装配不当所致;
(3)磨损后间隙扩大。液压冲击问题是指由于液压冲击所产生的瞬时压力往往比正常压力高好几倍,而导致密封圈损坏、接头与法兰松动、元器件原始强度恶化等现象。温升发热问题是指由于油温升高,而导致油液粘度下降、油液变质、密封圈硬化膨胀等现象。
4.工程机械液压系统防泄露技术措施
(1)提升加工、装配技术。
(2)优化液压系统设计方案。
(3)减少油管接头。系统泄露30%-40%是管接头泄露的,减少接头能有效降低泄露发生的概率。
(4)健全管理制度。有计划的定期检查、更换、维修液压设备。
(5)选择合适的液压元件。
(6)控制液压系统的油温。
(7)防止液压设备受机械振动和冲击压力。总之,液压系统的防泄漏是当前一个重要的研究课题,不能够单纯的依靠密封来解决,而要从总体上去消除泄露的根源。消除泄露应立足于防,适当堵、导,积极利用。
篇6:浅析液压系统漏油工程机械论文
浅析液压系统漏油工程机械论文
1系统漏油的原因及排除方法
1.1管路漏油
因为管道安装不符合标准,技术人员在进行软管安装时正常情况下,弯管的半径应该大于等于胶管外景的十倍或者是内径的15倍,同时弯曲处距离管头的长度也有着十分严格的要求,通常要大于外径长度6倍以上,。如果在安装中小于这些数据,系统的耐压程度就会受到极大的影响,在安装的过程中如果要求按照小半径进行安装,就一定要选择质量更好的胶管,同时在安装的过程中还不可以出现液压管拧扭的现象,以防止液压管出现爆裂的状况,软管要保证其整个呈一条直线的情况下才能得以正常使用,胶管接头在进行拼接的过程中不能用力拉伸,在管的预留长度上也应该达到相关的标准和要求,所以在胶管长度上缩量大约要控制在2%,而伸量大约要控制在4%,在安装胶管的过程中,胶管不能靠近热源,如果违反这一规则,胶管就很有可能因为长期处于高温环境而发生爆裂的现象,如果在安装的'过程中必须靠近热源,一定要在胶管上安装隔热板。再次是操作不规范。如果在操作的过程中因为换向阀的操作速度过快,就会出现油缸和马达无法正常工作的现象,液体的流速和流向在这时都会发生很大的转变,这样就会使得液体对系统的压力比正常运行过程中的压力高出两倍甚至更多,这种压力音速传播到液压系统的每一个部分,最终形成一股较大的冲击力,在这一冲击力的作用下,液管很有可能因为无法承受冲击力而产生损坏的现象,这样也就使得液管出现漏油的情况,需要注意的是,在维修的过程中如果液压管的内部有明显的腐蚀现象,并且已经超过管壁厚度的10%,就需要在维修中更换新的管道。最后是管道接头部分漏油。液压系统最容易产生漏油情况的部分就是管道的接头位置,产生这种现象的主要原因是接头的密封工作存在着一定的问题,封油的压力相对较小,如果出现这样的情况,可以将管道重新拆卸进行二次安装,拧紧就可以改善这种现象,在密封的过程中,尽量不要选择使用塑料作为密封的材料,因为如果使用塑料密封材料会使油渗透到管道中形成比较顽固的污渍,这样一来,密封面的清洁程度就会受到很大的影响,从而也加重了漏油的情况,如果油中本身就含有大量的杂质就会使得密封构件和摩擦面的磨损加重,从而也使得密封件的使用寿命大大缩短。另外因为安装不当也会使得密封件的实际作用受到严重的影响,造成了比较严重的漏油现象。
1.2密封表面处漏油
(1)密封件老化:密封件长期使用超过其寿命时会逐渐老化变质失去弹性,使封油压力低于工作压力,造成密封面处漏油。
(2)密封件设计不合理或安装不当:当工作压力较高时,易将密封件部分挤压于零件之间而损坏。其挡圈常选用摩擦系数很低(约为0.02)的聚四氟乙烯夹布胶木、尼龙6或尼龙1010来制作。另外,在安装时如果使油封扭曲、刮伤等都会降低密封件寿命和封油性能。
(3)密封件预压量过小或不均:密封件预压量增大时,其封油压力增大,密封性好;预压量过小或不均时易产生漏油。但过大预压量会降低密封件寿命。
1.3元件的内泄漏
内部漏油很难发现,在多数场合下,可由回路图确定。在给定条件下,哪些油口应和压力源脱开,如果拆掉与油口连接的管子,把这个油口敞开,而从油口流出的量很明显,则必有内部泄漏达到这个油口。回路图还能说明哪些元件构成了从压力管到通油箱的回油管的漏油通路。通过对以上步骤的检查,便可发现某一元件内泄漏严重,应及时维修、更换,以便提高该液压系统的机械效率。
2工程机械作业时的注意事项
2.1要有效地避免产生冲击负荷
液压阀开、闭不能过猛过快;避免使工作装置构件运动到极限位置产生强烈撞击;没有冲击功能的液压设备不能用工作装置(如挖掘机的铲斗)猛烈冲击作业对象以达到破碎的目的。另外,因为每台设备操纵系统的自由间隙都有一定差异,连接部位的磨损程度不同因而其间隙也不同,发动机及液压系统出力的大小也不尽相同,只有使用该设备的操作手认真摸索,修正自己的操纵动作以适应设备的个性,经过长期作业后,才能养成符合设备个性的良好操作习惯。
2.2严格执行交接班制度
交班司机停放机械时,要保证接班司机检查时的安全和检查到准确的油位。系统是否渗漏、连接是否松动、活塞杆和液压胶管是否撞伤、液压泵的低压进油管连接是否可靠、油箱油位是否正确等,是接班司机对液压系统检查的重点。
2.3保持适宜的油温
液压系统的工作温度一般控制在30~80℃为宜(危险温度100℃)。液压系统的油温过高会导致油的粘度降低,容易引起泄漏,效率下降;加速机械的磨损;生成碳化物和淤渣;油液氧化加速油质恶化;油封、高压胶管过早老化等。
2.4液压油箱气压和油量的控制
压力式油箱在工作中要随时注意油箱气压,其压力必须保持在随机5使用说明书6规定的范围内。压力过低,油泵吸油不足易损坏;压力过高,会使液压系统漏油,容易造成低压油路爆管。对维修和换油后的设备,排尽系统中的空气后,按随机5使用说167公路与汽运明书6的规定检查油位状态,将机器停在平整的地方熄火15min后重新检查油位,必要时予以补充。
3结论
液压机械已经在很多领域都有了比较普遍的应用,但是在液压系统的维护工作中也存在着一定的问题,漏油现象是比较常见的一种故障,为了更好的保证系统的正常运行,必须要对产生漏油现象的原因进行分析,同时有针对性的采取措施进行妥善处理,这样才能更好的推动液压系统在工程机械中的应用。
篇7:民用飞机液压系统油液污染及其控制分析论文
民用飞机液压系统油液污染及其控制分析论文
根据污染物存在的形式, 可分为固态污染物(固体颗粒)、气态污染物和液态污染物。污染物的上述三种状态在外部环境改变时, 可能相互转化。
1 固态污染物(固体颗粒)特性及危害
固体颗粒是引起油液污染及机械磨损排在第一位的因素, 也是污染控制研究的主要对象,世界各国都有广泛研究,总结起来有如下几个特性。
( 1 ) 细微性。
我们所研究的固体颗粒也是以微米为计量单位的物质, 肉眼可见的最小颗粒尺寸为40μm,不同类型的微小固体颗粒尺寸范围见表1。
( 2 ) 沉降性。
存在于油液中的固体颗粒都受到三种力的作用,一是重力,二是扩散力,三是浮力;当重力大于浮力和扩散力时,就会自然下沉, 称为沉降性。
( 3 ) 聚集性。
细颗粒粘结或聚集成团块的现象称为聚集性, 在大多数情况下是不利的。
( 4 ) 吸附性。
如同墙壁落灰一样, 油液在系统内流动时污染物也会附着在壁面上, 并逐渐增厚,当受到外界振动冲击后会一起脱落,造成集中污染。它比分散污染更为有害,甚至是致命危害。
如果颗粒的硬度等于或小于表面的硬度, 表面的磨损量就很小。只有当颗粒硬度大于金属表面硬度时, 才能对金属表面产生磨损;反之,颗粒硬度小于金属表面硬度时, 对金属产生的磨损作用是很小的。
( 6 ) 催化作用。
油液中的水和空气, 以及热能是油液氧化的必要条件, 而油液中的金属微粒对油液氧化起着重要的催化作用。试验研究表明,当油液中同时存在金属颗粒和水时,油液的氧化速度急剧增快, 铁和铜的催化作用使油液氧化速度分别增加1 0和3 0倍以上。
固体颗粒污染的危害主要表现如下。
1 . 1 运动件表面磨损引起功能失效
( 1 )液压泵和液压马达功能失效。高速运转中的配油盘与转子、柱塞与柱塞孔等部件,都是在大载荷、小间隙条件下工作,油中的固体污染物可破坏油膜,划伤运动表面。
( 2 )齿轮齿面磨损引起失效各种齿轮。在工作中是滑动和滚动同时存在, 而齿轮的主要工作状态是重载、薄油膜,大于油膜厚度尺寸的固体污染物又都能进入齿面接触区,造成齿面的剧烈磨蚀,硬度大的颗粒划伤更为严重;此外,重载摩擦的瞬时高温可使齿面产生凹痕, 反复工作使表面疲劳破坏, 引起机械失效。
( 3 )其他元件表面破坏各种类型的运动件。如轴承、油缸筒、阀类以及密封装置等,都会因油液污染并在高压、高温和高速条件下不断破坏工作表面, 到一定程度引起功能失效。
( 4 )密封胶圈的破坏胶圈是流体系统不可缺少的密封装置, 密封件的寿命与油液固体污染度息息相关,污染度越高,固体颗粒嵌入胶圈摩擦面的机会越多, 造成胶圈被划伤、剥落。
1 . 2 金属颗粒促进油液氧化变质
由于油液中进入水份和空气, 可引起油液乳化,也可产生微生物和胶质状物质,更易引起酸碱度的变化, 尤其是在某些金属微粒的作用下产生严重的腐蚀, 还可能产生偶发故障。
1 . 3 堵塞网孔
因油液变质生成微生物和各种胶状物质,可堵塞各类滤油器的网孔,造成滤油器功能提前失效;油滤失效后,可引起微孔被堵塞,或者是伺服阀的喷嘴挡板被堵塞,造成伺服控制系统失去控制功能, 酿成严重后果。
1 . 4 油液粘度变化
粘度是液压油的重要指标, 要求能满足低温条件下顺利起动, 也可以保证高温条件下的润滑性能,在水、空气和金属微粒的作用,破坏了油液的理化性能,也破坏了油液的粘度指标,无法满足高、低温条件下的.工作需要。
2 水污染特性及危害
液压系统难免在不同程度上存在着水份。水可以溶解在油中(称为溶解水) ,也可以自由状态存在于油中(称游离水)。自由状态水可以是沉淀水或乳化液; 沉淀水由长期静止的水珠形成, 存在于液体的底部或顶部,这取决于它们的比重。对矿物油,水一般沉淀于底部, 对磷酸酯或含氯碳氢化合物等合成液,则浮于顶部。在充分搅动的情况下,如通过泵的多次循环,水与液体可组成乳化液。
水对液压系统的危害也是相当严重的,它可使油液粘度下降,破坏油膜,引起严重的机械磨损;可产生酸性物质,增加油液的酸值,对系统增加腐蚀;在低温下,游离水常以冰块形式存在, 会引起运动件被卡住;水的含量超过3 0 0 p pm就可以引起碳素钢或合金钢生锈,造成滑阀被卡死,操纵系统无法正常工作, 现实中发生过因水污染飞机起落架放不下的故障。
3 空气污染特性及危害
液压油中溶解空气是不可避免的, 液压油中空气溶解量是依压力和温度的不同而不同,随着压力的增加,各种液体饱和溶解度都是呈线性的增加,同时又随温度的降低而不同程度的减小。
正因如此, 在液压系统中不同位置其压力是不同的,随着压力的降低,超过饱和溶解度的空气就会逸出成游离态, 而当压力升高时又溶解, 所以空气在系统中有时溶解有时逸出, 这种时隐时现的变化过程对系统有很大的危害, 是系统中的顽症。空气在液压油中也是两种状态存在,一是溶解在油中,一是以游离状态存在。以游离状态存在对系统的破坏最为严重。其危害主要表现为:
3 . 1 降低油液的弹性模量
当油液中有游离气体存在时, 就大幅度降低油液的弹性模量。例如:液压油在无游离气体时弹性模量平均值为1 5 1 0MP a ,如果夹杂空气,油液的弹性模量会降到3 5 3M P a以下,能造成系统响应迟缓,工作不稳定,会影响飞机操纵的跟随性,影响操纵力的稳定。由于这一故障的发生是随机的,有太多的不确定性因素, 造成故障现象不易再现, 也为故障分析工作造成困难。
3 . 2 产生气蚀
当系统的油液由低压区进到高压区时,气泡会瞬间被压缩破灭,此时产生的局部高温和高压冲击, 造成元件表面恶化和剧烈振动,气泡破裂会产生巨大的冲击力。
3 . 3 引起电液伺服阀工作失灵
现代飞机大量采用电传操纵, 大量应用电液伺服阀, 以实现快速准确的改变飞机姿态,而当油液中有微小气泡出现时,气泡会影响节流孔的通油能力, 可影响力矩马达的正常工作, 造成伺服阀工作瞬间失灵,影响操纵特性,自动化程度越高此项问题越突出。
3 . 4 增加系统的温升
当油液中气体含量太多, 低压区必然游离出气泡, 而气泡被压缩耗费的能量转变成热量,引起系统温升严重,温度过高会带来一系列弊病,例如:胶圈老化,系统漏油,油液润滑性能变差引起磨损严重,有资料介绍,当系统中油液温度降低8℃ ,油液寿命即可延长一倍。
3 . 5 促进油液氧化变质
空气含量增多必然对油液产生氧化腐蚀,增加油液的酸值,缩短油液的使用寿命。此外,气泡可破坏油膜,造成摩擦副失去润滑, 既破坏了摩擦表面又生成了大量污染颗粒, 等等。总之系统中空气含量增加, 给系统带来的危害是巨大的。
4 污染控制及设计要求
系统污染度控制, 材料选择和结构设计各环节都十分重要。
4 . 1 结构设计中应贯彻提高附件污染耐受度原则
应合理的选择间隙和最小孔径, 尽可能降低因污染所能引起的严重后果; 在选择材料和磨擦副时应贯彻低污染生成率原则, 因低的污染生成率是降低系统污染度等级的关键环节。除产品交付之前就带进系统的污染物以外, 污染物主要是在工作过程中生成的, 关键的摩擦副应选择有试验结论的材料和参数。
4 . 2 过滤设计
过滤设计是系统设计时不可忽视的重要内容, 首先是装机滤油器的参数选择和配置方案, 其次是采用地面净化装置定期净化。
将系统工作中自身生成的和外面侵入的各种固体污染物从油液中清除, 最普遍使用的方法是过滤。利用多孔性的介质滤除油液中非可溶性固体颗粒的元件称为滤油器。滤油器可分为表面型和深度型两大类, 表面型滤油器的通孔认为大小是均匀的,因而,所有大于通孔尺寸的污染颗粒均能被堵截在表面, 而小于通孔尺寸的颗粒均能通过。深度型过滤器的过滤元件为多孔性材料,内有曲折迂回的通道,对固体颗粒的清除主要是靠堵截沉积和吸附作用,深度型过滤器过滤介质的孔径是不均匀的, 它的过滤作用有更大的机率性。
4 . 3 推广采用封闭式油箱
液压油箱中的油液与空气直接接触,即开式油箱, 是外界污染物进入液压系统的主要渠道, 尽管开式油箱都加“ 呼吸器”阻挡空气中灰尘进入, 但是这种滤网起到的作用仍然有限。另外,大气中的水分和空气都通过开式油箱进入系统, 它的危害在前面已经阐述。采用封闭式油箱,隔绝油液与大气的通道, 是堵截污染物侵入系统的有效方案。
5 结语
通过对各种污染物的分析和研究有利于系统设计时更好地实现污染度控制的目标, 以保证飞机液压系统平稳、安全、有效地运行。
篇8:工程机械热管理系统设计方法论文
工程机械热管理系统设计方法论文
1热平衡分析
热平衡状态下,各处温度保持恒定不变,各系统的吸、放热量相等。(1)发动机冷却系统Q0=Q1=P1,式中:Q0为冷却液通过发动机时的吸热量;Q1为冷却液通过水箱散热器时的放热量;P1为水箱散热器的换热量。
(2)液力传动散热系统Q21=P2,式中:Q21为液力油通过液力散热器时的放热量;P2为液力散热器的换热量。Q21+Q22=Q2,其中Q22=∑KdiAdiΔtdi。式中:Q22为液力系统油箱、变速箱和输油管路等表面的放热量;Q2为液力变矩器的液力损失;Kdi、Adi和Δtdi分别为液力系统油箱、变速箱和输油管路等表面的散热系数、外表面面积和油与环境的温度差。
(3)液压传动散热系统Q31=P3,式中:Q31为液压油通过液压散热器时的放热量;P3为液压散热器的换热量。Q31+Q32=Q3,式中:Q3为液压系统的能量损失;Q32为液压系统油箱、液压缸和输油管路等表面的放热量。
(4)冷却风散热系统Q4=Q1+Q21+Q31=P1+P2+P3,式中:Q4为空气通过散热器组时的吸热量。虽然传统设计方法存在对细节考虑不足的缺点,但其具有对问题表达方便以及计算过程简单等优点,对某些问题也不失准确性,故仍作为设计和研究热交换系统的基本方法,具有较大的使用价值。
2试验研究
试验研究是利用先进的物理试验技术,对实际热管理系统关键部位的主要工作参数进行测量分析。任何理论计算方法都是建立在某些假定条件上的抽象方法,都有其适用范围,偏离了其适用范围,计算结果就会产生较大偏差。由于流体传热问题的复杂性,人们目前对某些方面的认知还不够深入和准确,试验研究仍是不可缺少的手段。试验测试系统结构如图1所示[5]84,88[7]20。
3流场的`数值模拟分析
工程机械主要利用流体来完成传热,流动特征对传热效果和能量损失有着较大影响,合理设计流道是非常必要的。随着计算流体动力学(CFD)技术在传热方面应用的不断深入,利用数值模拟计算分析流场,可获取大量的流动细节数据,有利于分析产生不良性能的原因。可利用CFD技术对冷却风流场、散热器中流体流动及传热特性、发动机冷却水腔内部流动、液力变矩器以及液压元件内部流动等进行分析。引入CFD技术可弥补传统设计方法的不足,并降低开发成本和缩短开发周期,它已成为国内外自主创新和自主设计的重要技术支持之一[5]8[6]4[7]20,501。例如冷却风流道由机罩、发动机、导风罩、风扇和散热器组构成,其中流动比较复杂,不同部位流态差别也较大。在设计机罩、导风罩和风扇等时,可以借助CFD软件对流场进行数值模拟分析,由此对上述部件的结构形状进行优化改进。利用冷却风流场的数值模拟结果,还可以计算出冷却风的平均集总参数,用于对整机热管理系统的计算机仿真分析[10-11][12]092802-6。
3.1流场数值模拟分析
对流场进行数值模拟分析主要包括建立计算域、计算域网格划分、流场数值模拟计算和计算结果分析。目前常用的CFD软件有Fluent、STAR-CD和CFX等,由此进行数值模拟计算大多可以得到比较满意的结果,其中准确设定流体密度和黏度等物性参数以及边界条件是获得准确计算结果的关键[7]507。计算结果分析包括以下内容。
(1)流场分析观察分析流速及压强等物理量的大小及分布特点,分析流场中涡流、滞流、回流、卡门涡列等流动特征的位置和强度,分析它们对工作性能的影响。
(2)典型断面主要参数的分析利用流场模拟计算结果,可计算出平均流速、平均压强、流量和阻力等参数,进而可计算出流速系数和阻力系数等参数。据此分析流动参数与流道几何结构、尺寸以及工作参数之间的相互影响,为设计高性能产品提供有价值的建议。
3.2装载机冷却风流道的分析
针对XG953型装载机,利用CFD技术计算了原结构和几个改进方案的冷却风流场。重点从流速场、压力场、流量和风阻4个方面进行比较分析,由此提出改善散热效果的措施:
①封堵或尽量减小散热器四周的间隙,避免热风回流;
②机罩后部靠顶部处开出风口,以保证热风排出顺畅;
③进风口采用风阻较小的网状结构,其位置尽量靠近风扇进口,以减小进风风阻。采用前两个措施后,可增加冷却风有效流量约15.2%。采用某一改进方案,在高速跑车工况下,装载机机罩出口冷却风速度分布如图2所示。将机罩出口冷却风速度的计算值与试验测量值比较发现,计算值与试验测量值基本接近,表明采用数值分析方法能很好地解决实际问题。
4计算机仿真
工程机械热管理系统由多个子系统组成,实际工作中它们之间相互影响,单纯依靠传统计算分析方法,不易设计出整体性能良好的热管理系统。因此,借助先进的计算机系统仿真技术,对整机热管理系统的工作特性进行模拟计算,无疑是解决这种复杂问题的有效手段。利用计算机仿真技术,可以计算出系统中各个部位的温度、压力和流量等参数的静态和动态特性,可以分析各参数对各子系统的影响以及各参数对系统性能的影响,有助于人们对系统更直观、更全面、更深入的认知,弥补传统计算方法和试验的不足。可用于该方面的仿真软件有EASY5、Flowmaster、MATLAB/Simulink和20-sim等[14]。
4.1XG953型装载机散热系统仿真模型
笔者利用EASY5软件构建了改进后的XG953型装载机散热系统仿真模型,散热系统包括发动机散热、液力传动系统散热、液压系统散热和冷却风4个子系统,如图3所示。
4.2仿真结果分析
在36℃环境温度下,对装载机在高速跑车工况下的热平衡状态进行了仿真计算与试验测试,结果基本吻合(如表1和表2所列)。其中发动机冷却水和液力传动冷却油的热平衡仿真曲线如图4所示。
5结语
在工程机械热管理系统设计与研究中,集总参数计算分析主要是基于流体力学和传热学中的束流理论,计算分析平均流速、压力、温度、流量和换热量等参数;试验研究是利用物理试验技术,对实际系统的主要工作参数进行测量分析;流场数值模拟分析是利用计算流体动力学技术,计算系统中零部件的内部流场,分析流动特征,研究流动参数与流道几何结构、尺寸以及性能参数之间的关系;系统的计算机仿真分析是对整机热管理系统的工作特性进行模拟计算,研究工作参数与系统性能的关系。采用整体系统设计与研究思想,将集总参数计算分析、试验研究、流场数值模拟分析和系统的计算机仿真分析有机地结合起来,建立一套比较完备的现代设计与研究方法,对整机热管理系统设计改进具有很好的指导作用,可更有效地解决工程机械热状态不佳的问题,消除产品质量隐患,提高其动力性、经济性、可靠性和使用寿命。
篇9:工程机械液压系统的控制方式论文
【摘要】我国的水利水电工程的施工技术较为复杂,河道的截流问题作为一个关键的步骤被工作人员给予了高度重视。河道截流问题在具体的施工中是非常有难度的,并且也存在一定的危险系数,为了保障施工人员的生命安全以及施工的顺利进行,必须对现场的施工环境和条件进行仔细的盘查,有效的完成施工的进度,保证施工的质量。
【关键词】水利水电工程;施工;河道截流技术
1截流工程施工概述
河道截流技术就是在龙口形成后,对龙口采取一定的措施进行防护。在龙口进行防护之前要采取相应的准备工作,在不影响航运的季节,安全措施达到标准的情况下进行截断河流。河流截断之后,要想没有后顾之忧,必须投抛防渗材料。为了消除以后的安全隐患,避免因洪水等自然灾害而导致围堰破损,应该提前进行加固加高工作,河道截流工程的实施与众多的自然因素与人为因素息息相关,施工之前必须对当地的地质环境,人文环境进行严密的考察工作。准备施工前的材料,召集有关工作人员进行河道截流工程的方案设计,在准备好实施方案后,还要随机应变的准备突发事件急救方案,已做好完全之策,不得耽误工程的实施进度。
2河道截流的现状
我国经历了大大小小的数十起河道截流工程的实施,积累了相当丰厚的经验,加快了施工的进程,根据有利的地形进行爆破式的就地取材。这种方法要考虑到是否存在安全隐患,在保障安全的前提之下,节省资源和运输的成本。现阶段,我国大部分的水利水电工程的实施采用高度机械化投块料截流的方法。由于水位差和水流速等影响因素的存在,大多以平堵法进行河道截流方案的实施。投抛料随着经验的积累和为提高使用年限,综合各方面的利弊,现在从普通的石块进行投料改成使用混凝土等材料进行投料。
3截流方法的运用
单戗立堵截流,这种方法在实施过程中比较简单易操作,但是适用的范围是有一定局限性的,在施工的过程中,截流的水位落差尽量保证在3.5米左右。当水位落差在3.5米以上时,可以采用另外一种截流方法:双戗和多戗立堵截流。但是这种截流方法的经费较高,在物料的消耗上较大,技术操作方面比较繁琐,需要大量的操作人员进行检测和操控,耗时又耗力。另一种情况,当解决漏水问题,必须在戗堤上设置防渗水的设备。同时要对河床进行加固,这种一举两得的办法可以采用立堵法截流,这种截流方法不需要进行架设浮桥或栈桥,没有较为繁琐的操作步骤,节省了相当大的一部分物料,节约了成本和物资。我国大部分的水利水电工程中的河道截流方法大多数都采用立堵法截流。另外一种施工时间较为短的截流方法叫做平堵法,平堵法截流在施工之前必须进行浮桥的架设,在材料的选用上要选择较为轻盈的材料,在施工的速度上要比前几种截流方法要快,但是由于浮桥的架设,在一定程度上会有碍交通。
4龙口位置的选择
龙口位置的选择要进行施工环境的有效勘测,从地质条件来看,龙口本身就要进行投料堵塞,堵塞完成后,由于水力有一定的冲刷作用,并且水流的重刷力度决定了投放材料的使用年限,所以在龙口位置的选择上要首先考虑到河床的抗阻击能力,分担水流对龙口的冲击力。龙口最好是选在便于投料能够稳固的立于水中的位置。在有利的地形中便于就地取材,龙口应选在距离材料产地较近的位置,这样减少了运输费用,减小了施工的难度,方便了爆破的实施。
5根据龙口设计选用截流材料
龙口的宽度一般是为60.0m左右,龙口进占分三个区:不同的区位的龙口的流速也是不同的。河道截流中选用的材料一般为了方便运输,进行就地取材,可采用爆破的技术对河岸两旁进行爆破取材,粘土的获取只要在料场覆盖层进行挖掘。在水位较深的地带,投抛材料的选用一定要坚硬结实,根据经验,一般选用土石料。但是弥补一种缺陷的同时也会造成其他方面的缺点的暴露。堤头的坍塌是与土石料的采用息息相关的,这种材料的遇水凝合力会下降,容易发生坍塌事故,存在较大的安全隐患,在操作上也存在一定的难度。材料的形状也是对河道截流的质量有一定的影响,在施工的过程中必须要保证施工材料的稳定性良好,一方面要保证施工人员的.人身安全,另一方面要保证施工的进程。为了满足以上两个方面的要求,在河道截流材料形状的选用上一般采用圆柱形。首先在材料的搬运上就省了相当大的力气,圆形的材料不用采用蛮力搬运,利用巧劲即可直接滚入水底,稳定性方面也是相当有保障。在建造上,圆柱形材料比较省时省力,节约成本,减小了开支,增强了河道截流施工中的安全系数。在选用材料上一般遵循以下原则:截流抛投材料选择原则:(1)首先考虑安全因素,在消除安全隐患的条件下,结合的当地的地形进行就地取材,开发天然渣料,节省成本和资源,减少不必要的额外开支。(2)填充龙口的材料要进行数量的估算,以免在投放的过程中对堤坝造成不必要的损坏。要以堤坝的承受力度作为首要的考虑因素。(3)河道截流材料要有备份,不能只根据预计方案贮备材料,为应变突发时间,要储备大量的材料进行应急备用。
6河道截流时间的确定
导流泄水建筑物必须建成或部分建成,是进行河道截流工作之前必须进行确定的两项指标。在施工之前,堵塞在河道中的淤积物或者其他与工程实施无关的一切障碍物都要进行清理。在进行河道截流时也要考虑各方面的因素,比如要考虑截流阶段的航运情况,一般货物的运输都是有季节性的繁忙阶段,要尽量在避开航运比较繁忙的时期进行河道截流工程的实施。河道截流时要考虑到水位的落差,在河道截流之前,要进行浮桥或者浅桥的搭设,一旦水位过高,搭设浅桥用的材料和物资就相对来说较高,这还不是关键点,水位较深或者水流较急,截流材料的抗阻击能力就会减弱,稳定性就会减弱,直接影响到施工过程中的操作人员的人身安全,间接的影响到了施工的质量和施工的进程。所以综合以上的安全隐患的存在,河道截流的时期一定要选在河流的枯水期,再结合具体的天气状况进行最后的河道截流的方案和时间。
7截流流量的设计
截流设计流量首先要考虑的就是龙口的尺寸大小。一般截流量为该月水流速率最大时的百分之五为依据来设计。在制定万截流量后,可根据不同时间段内的水流速度和流量进行记录分析,进行最终标准的制定。这种实施方案对于水域面积较广的区域应用较为广泛。在确定截流量的时候一定要多进行数据的采集,保证截流量的正确设计。
8结语
综上所述,河道截流受河道流量、地质因素、气候环境等因素的影响。因此,在水利水电工程的实施前,一定要做好充分的调查,多加参考往年的水流量和水流速度,对各项影响因素进行全面的数据分析。对每一个在河道截流过程中可能遇到的问题作出相对应的预案,保障施工人员的人身安全,解决施工过程中的疑难问题,才能有效的保障施工的顺利进行。
参考文献:
[1]李建.水利工程施工导截流控制要点分析[J].广东科技,.
[2]李中成.周朝波.水利工程中导截流施工工艺[J].科技创新与应用,2014.
篇10:如何正确维护好常用工程机械液压系统论文
如何正确维护好常用工程机械液压系统论文
常用工程机械液压系统是由阀门、泵体等部分构成,由于其构造的形式,导致其故障率比较高,常见的故障为液压离合器接触不是很好或者是机械液压系统的动力严重不足等液压系统的问题。工程机械液压系统产生这些故障无非来自于控制阀和液压缸活塞系统的局部缺陷或局部破损。
1工程机械液压系统的常见检查方法。
结合液压离合器接触不是很好和机械液压系统的动力严重不足两个问题,简要谈谈如何检查常见工程机械液压系统,结合多年从事此行业的经验,笔者自己总结了几个方法:
①直接观察,再根据经验判断故障出在什么地方,这种方法对检查人员的综合素质要求比较高。这种方法的缺点是对于复杂的工程机械液压系统的复杂故障,通过这种方法是很难被发现的,只能采取别的方法。
②零件置换法,此种方法适用于维修现场缺乏响应的检测仪器或被检查的原件拆不开的情形,把怀疑有故障的零件拆下来,换新零件进行试验,采取这样的排除的方法,来检查出故障的零配件;
③实际测量法,顾名思义,这是通过对工程机械液压系统的检测并分析其结果从而得出故障原因结论的一个常用的方法,但是由于电子测量仪器,有它的误差范围,通过直接测量的结果,有可能出现误差,这种方法受外界环境的影响大,尤其是温度、风力、天气等原因,而这些原因又是人类难以很好控制的,所以这种方法只能作为一种参考,为工程机械液压系统的故障判断,提供一个诊断方向。
④推断法,这种方法的思路就是,利用工程机械液压系统的原理进行推断,逐步排查出故障出现的可能原因。实际工作中,都是通过这四种方法的有机结合来判断系统故障的原因及部位,由于机械液压系统的复杂性尽量不要妄自下定论,一定要综合起来考虑。所以,在常见工程机械液压系统故障的检查过程中,要求相关人员要具备很高的综合素质与能力。
2工程机械液压系统的维护。
下面结合常见工程机械液压系统的的主要故障类型,简要谈谈工程机械液压系统的维护。
现在我国常用的工程机械液压系统的动力都采用的是液压油,液压油的品质关系着工程机械液压系统的维护效果与工程机械的使用寿命,质量好的.液压油可以延长工程机械的有效使用寿命与经济寿命,从而节约了工程机械的运行成本,提高效率。但是液压油有着严格的等级区分,在使用时应该按照相关的文件规定选用相应的规格型号的,质量靠的住的产品。要选择那些正规的厂家生产的,具备相应的合格证的及有法定资质检测单位提供的检测报告的液压油产品。所以,使用液压油,绝对禁止不是一样的型号,不是一个牌号的液压油混着用,其主要是因为液压油与液压油之间会产生化学反应,可以导致其化学、物理性能发生变化,失去使用的效果。另外,变质的液压油严禁在工程机械上。密切关注智能装置传回来的数据,现在大部分工程机械都装有智能回传系统及智能装置,智能系统能警示液压系统的故障部位,要密切关注其提供的数据及情况,但是毕竟是电子系统,电子产品的监测范围和检测结果的准确性有一定的误差,在工程机械液压系统的维护过程中,一般是将电子产品装置的回传数据与定期对工程机械液压设备进行检查和保养相结合,才能达到最终的目的。
对于阶段性的保养,250H时,应该着重检查滤清器上的杂物,如果滤清器滤网上的金属粉末比较多,必须查明真正的原因并采取相应的措施后才能够再运行工作,如果滤清器的过滤网有破损,在不能进行修复的情况下,更换新的滤网,然后再投入工程机械中使用。500H时,在工程机械液压系统正常运行500H后,应更换滤清器滤芯,如果工程机械液压系统长期在高温及复杂的环境下工作,应在工作不到500H时,提前更新滤芯,以保证工程机械液压系统的正常运行。1000H时,此阶段为关键性阶段,在工程机械液压系统正常运行1000H后,应该更换滤清器上的滤芯、更换液压油、清洗滤清器,如果工程机械液压系统长期在高温及复杂的环境下工作,应在工作不到1000H时,提前做这些工作.对于7000H和10000H的检查维护,这是一个比较长的时间的磨合,所以在这个阶段的维护要让技术人员操作,大量的调查数据表明,及相关资料的查询,工程机械液压系统运行10000H后,其液压马达、液压泵等主要部件要进行大修,不然的话,很容易损坏,对整个系统是致命性的破坏。
在常用工程机械的日常使用和维护过程中,要防止固体杂质进入工程机械的液压系统中,应为洁净的液压油是维持液压系统稳定运行的关键性因素,液压系统中存在大量的小精密构件,构件与构件之间留有很小的间隙和孔洞,假如固体杂质进入液压系统中,直接对系统的正常运行造成严重的影响,影响工程机械的使用。所以在换液压油时,必须保证液压油的清洁度以及加油工具的清洁,操作人员应配备专用的干净的手套及工作服。换液压油及零部件和保养时,应防止扬尘污染等。
在常用工程机械的日常使用和维护过程中,还要防止空气和水入侵液压系统,具体的措施有:在保养后要按《工程机械使用说明书》的规定排空液压系统中的气体;油泵的驱动轴应该密封好,吸油管密封好;驱动轴处油封要使用双层油封,不得使用单层油封;储油桶在不使用时,要密封,倒置放置等。
3注意事项。
在常用工程机械的日常使用中,应注意:避免粗暴,操作手应稳定,因为经过长期作业后才能培养出操作手符合设备情况的良好的操作习惯,所以工程机械行业要坚持定人定机的制度;注意气蚀和溢流噪声,在工程机械作业中,如果出现异常的噪声,应查明噪声的来源,如有必要,要进行停机检修;严格执行交接班制度;保持适宜的液压油温度;液压油箱气压和油量的控制到位等。为了使工程机械液压系统的使用时间更长,在制定使用制度时,必须要定人、定机、定地点。责任到人,责任人应正确使用机械,并严格遵照安全技术操作规程正确操作机器,并加强对相关人员的教育和指导,实行奖罚机制等。
随着液压系统在工程机械上的应用越来越多,工程机械液压系统的维护也被提上了日程,工程机械液压系统维护涉及到的学科领域和技术门类很广,要求相关人员要具备丰富的知识结构和实践经验,所以,在今后的工作中,我们要牢记工程机械液压系统的维护要点,并付诸于实践中,以保证工程机械液压系统的正常运行。
参考文献:
[1]颜荣庆。液压与压力传动[M].北京:人民交通出版社,.
[2]李自光。现代工程机械液压系统高温的分析[M].北京人民交通出版社,.
[3]王辉.工程机械液压系统泄漏的危害及控制方案[J].交通世界(建养・机械),,(Z1)。
[4]李海英。工程机械主动维护的要点[J].工程机械与维修,,(1)。
[5]张磊。实用液压技术[M].北京:机械工业出版社,2011.
篇11:工程机械液压系统的控制方式论文
工程机械液压系统的控制方式论文
引言
工程机械在连续作业中,其作业负荷的变化比较大。例如,推土机在作业时,作业负荷会从0变到无穷大,在这种情况下,发动机为了满足大负荷下的动力要求以及小负荷下的经济要求,就必须对其所输出的功率进行调整。同时,工程机械在操作过程中,一般需要协同作业。例如,在挖掘机进行装车作业时,动臂、斗杆、铲斗和回转需要协同作业,因而需要对工程机械的传动和控制系统做出调节,使其驱动部件的位置,满足速度需求。此外,在工程机械工作中,机械被要求既能够进行大功率输出,也能够进行精细化动作。比如,起重机在进行吊重时,要做到大功率输出,在吊装时,又要实现微动作。综上所述,工程机械的传动和控制系统需要具有良好的动力性、经济性、和调速性。
1工程机械的液压传动与控制系统分析
液压系统在获得能源时,需要将发动机输出的机械能在液压泵的作用下转化为液压能。液压泵输出的能量,会受到液压阀的调节和分配。系统的压力、流量和方向也会受到液压阀的调节和控制。此外,液压阀还可以对功率支流的绝对值和相对值进行控制。在机械能转化为液压能后,液压马达和液压缸又会把液压能转化为机械能,以达到操作机械工作的目的。如果要实现对工程机械的动力、节能、和作业效率的控制,就需要通过调节液压泵的排量和发动机的转速以及控制阀的开度来实现。
2液压系统的功率控制方式分析
压力和流量是液压系统的功率形式,液压功率用公示可以表示为:P0=pq/60,在式中,P0为液压功率;p为液压系统压力;q为液压系统流量。液压系统工作时,负载的大小决定了其压力的.大小,因此压力不是其液压系统固有的参数,压力是载荷的一种反应,而真正能够对液压系统功率起到控制的是液压系统的流量。因此,下面分别从液压泵和液压阀的流量控制来进行分析。液压泵流量公式:q0=V.n,式中q0为液压泵流量;n为液压泵输入转速;V为液压泵排量。
要改变机械的速度,就要改变其流量,而从公式中可以得知,流量的改变可以由改变液压泵的排量和转速来控制。如果采用液压泵转速进行调节,称之为变频调速,如果采用液压泵排量进行变速,称之为容积速调。在工程机械的工作过程中,由于外在负荷变化会使发动机的转速不稳,而柴油机的转速一般要求相对稳定,如果转速不稳,也要通过一定方式对其进行控制。因而,在控制液压泵的流量时,在假设其转速稳定的情况下,对液压泵流量进行控制。液压泵输出的流量由液压阀进行二次调节。在工程机械中,比例控制阀实际上属于可变液阻,并联液压回路的泵侧的压力是相等的,各支路的流量是由并联液阻的绝对值和相对值决定的,而这里的并联液阻是由液压阀构成的。液压阀的流量公式为式中,Q为液压阀的流量;Cq为流量系数;A为液压阀的开度;Δp为液压阀的压降;为液压油的密度。
从公式中知道,液压阀的开度和阀的压降决定了液压阀的流量,而液压阀的压降的决定因素是外部的负载,这种外在的负载是难以控制的,因此只有对液压阀的开度进行控制才能实现对液压阀流量的控制。但是,因为外在负荷因素的不稳定,液压阀压降的变化也比较大,造成的误差也难以控制,这种误差不仅大,而且,因为液压阀压降还跟机械装置的姿态和工作环境有关,其压降的变化难以通过其他手段来控制。所以如果是通过开度对液压阀的流量进行控制,从而控制执行机构的速度和位置是不理想的。
3液压系统的流量控制方式
通过以上分析可以得知,要实现对液压系统的流量控制,就需要对液压泵的排量和液压阀的开度进行调节,即泵控调速和阀控调速。泵控调速的过程中,液压系统不存在流量和功率的损失,泵控调速是以改变液压泵排量实现的,在调节液压泵的斜盘倾角时,推动斜盘、柱塞等原件和摩擦副需要一定的响应时间。阀控调速要实现对流量的控制,就要改变并联回路间的相对液阻,其中的大部分流量对外做功,多余的流量则回到油箱,多余的这部分流量就属于被浪费的流量。可见泵控调速比阀控调速的经济性能好。但是,在改变液压阀的开度时,通过将电磁铁推动阀芯就能实现,而且,液压阀的运动质量比阀芯的质量要大很多,其响应的速度会比较快。
在工程机械中,液压阀电磁铁的响应频率为10Hz左右,高速电磁铁的响应频率能超过20Hz,可见,这两种控制方式是优势互补。将二者的优势进行结合,就会成为一种不错的流量控制方式。而目前,先进的工程机械液压系统的流量控制就采用液压泵和比例阀结合的方式,形成优势互补,在液压系统作业时,首先是变量泵根据工作需求来确定首次排量,首次排量比需求的流量会多上20L/min以上,然后,比例阀会对流量进行二次修正,实现速度控制。采用泵控和阀控的方式目前有负流量控制,正流量控制,负载敏感控制。负流量控制见图1。从图1可以看出,采用负流量控制,主阀中位的流量控制着变量泵的排量,而且这两者的变化方向相反。正流量控制方式见图2。
从图2中可以看出,采用正流量控制方式,同一个信号在控制着液压泵的排量和液压阀的开度,而这能够有效提高液压系统响应速度。从图3中可以看出,采用负载敏感方式,主阀的压降控制着液压泵的排量,而压降与操作信号和最大的外在负载有关系,这种控制方式将操作者的预期速度和外负载速度限制结合在一起。在现实中,工程机械根据用途和要求的不同而采用不同的流量控制方式,如果是对响应速度要求不高的,就可以采用单纯的泵控系统,如起重机。如果对机械性能要求不高,但是要求快速反应,就采用阀控系统,如小型挖掘机。除此外,某些工程电子泵具有较高的响应特性、线性度和重复精度,可以实现对液压泵的精确流量的控制。某些工程用的伺服液压缸,可以实现速度和位移的精确控制。
4结束语
通过分析可知,要实现对工程机械液压系统的功率控制,主要是对液压系统流量进行控制,通过控制液压泵的排量和液压阀的开度,从而实现对流量的控制。而目前比较好的液压控制方式是结合了泵控和阀控的优点,实现操作的经济性和快速性。但是,工程机械中液压泵的排量因为是开环控制,排量的精度不高,而比例阀的流量控制精度受压力的影响比较大,可见泵控和阀控结合的控制方式在速度和经济上有不错的效果,但是在经济性上还存在缺陷,这也是以后工程机械液压系统发展的方向。
篇12:对于液压系统油液中气泡的防范研讨论文
对于液压系统油液中气泡的防范研讨论文
摘要:论述了气泡对系统的危害及气泡混入液压系统的主要途径,介绍了在液压系统设计和使用过程防范气泡危害的具体措施。
关键词:液压系统; 气泡; 危害; 预防措施
前 言
这些年来,对液压系统油液中的含气量,空气进入液压系统的形式以及液压系统油液中的气泡对液压系统工作的影响等方面,渐渐被国内外从事液压系统工作的研究人员所重视。在国内,一些从事液压技术研究的机构和大专院校正着手研究液压系统的这些问题。本文首先分析了空气进入液压系统途径,然后又在深入分析了气泡对液压系统运行所造成的危害的基础上,又论述了在设计、使用和维护液压系统的过程中防止气泡危害的具体措施,对液压系统的工作可靠性具有重大意义。
液压技术由于具有许多优点,在国民经济的各个领域中得到越来越广泛的应用。但是,液压系统性能的好坏,直接关系到液压设备能否长期保持良好的运行状态,关系到设备的故障和作业率,关系到设备的运行效益,乃至社会效益。因此,要保证液压系统具有良好的技术性能并保证正常运行,保证各执行器按照规定的要求平稳而协调地工作,合理的设计和正常的使用维护就显得十分重要。
1 空气是如何进入液压系统的
空气进入液压系统通常有混入式和溶入式两种方式 。了解空气进入液压系统的途径,在液压系统设计、使用和维护过程中有利于制定防止空气进入液压系统的具体措施,以避免或尽量减少气泡对液压系统的危害。空气进入液压系统与液压油箱工作状态有密切关系。许多液压系统与液压油箱是采用气-液接触式增压油箱,这将造成空气在液压油中的溶解度增大;液压油箱中的液面过低,加速了液压油的循环,使气泡排出困难,而且还将引起空气从外部进入液压油中;液压油箱台上的吸油管的位置设计不当也有关。所以在液压油箱设计中要注意上述因素,并尽可能在结构上采用一些措施。
空气的进入与液压油管的安装也有关系。若泵的进油管路漏气,则大量的空气会吸入;若系统回油管口高于油箱液面时,高速喷射的回油将空气带入油中,又经液压泵带入系统;各个油管接头密封不严或橡胶油管老化等使空气进入液压油中。
2 气泡对液压系统的危害
混入液压系统的空气,以直径0.05―0.5mm的气泡状态悬浮于液压油中,对液压系统的`液压油的体积弹性模数和液压油的粘度将产生严重的影响,随着液压系统的压力升高,部分混入空气将溶入液压油中,其余仍以气相存在。当混入的空气量增大时,液压油的体积弹性系数则急剧下降,液压油中的压力波传播速度减慢,油液的动力粘度呈线性增高。悬浮在油液中的空气与液压油结成混合液,这种混合液的稳定性与气泡的尺寸大小,对液压系统将产生重大的影响。
2.1 液压泵的工作性能变坏
空气进入液压系统以后,大大地恶化了液压泵和整个液压系统的工作条件,表现在液压泵性能变坏和寿命变短。当液压泵吸入了液压油和空气的混合油液,在液压泵的吸油管处,由于压力下降而析出已溶的气体,在液压泵高速旋转时,将造成油液不能充满油腔的现象,这不仅降低了液压泵的供油量和液压泵的效率,还会引起液压油液的冲击,液压的气蚀损坏,管道压力脉动,以至产生由于液压油的不连续流动而引起的噪声。例如,在实际工作中,就遇到过ZB-34液压泵在5000r/min运行时,没箱未增压和管路直径为20mm时,其液压系统的流量小于28L/min ,只有额定转速4000r/min下的额定流量的2/3,同时出现了较大的压力脉动,振动和噪声。这就是由于液压泵吸入了液压油与空气的混合油液导致液压油不能充满油腔而产生工作性能变坏。
2.2 产生噪声和振动
空气侵入液压系统是产生噪声和振动的主要原因。当溶有空气的液压油流进管路或元件的特别狭窄的地方时,速度急剧上升,压力急剧下降。当压力下降到低于工作温度下油液的气体分离压时,溶解于油中的气体迅速地大量分离出来,使油液中出现大量气泡。当气泡随油液流到压力较高的地方时,气泡被压缩而导致体积较小,此时在气泡内积蓄了一定的能量。当压力增高到一定数值时,气泡被压破裂,产生局部的液压冲击使系统产生振动,局部的压力可达几十兆帕,同时产生爆炸声。
2.3 液压系统不能正常工作
在液压系统中没有空气混入的情况下,其油液的压缩率约为(5―7)×10-3m3/N,可以认为油液是非压缩性流体,而不考虑其压缩性,一旦油中混入空气,其压缩率会大幅度增加,油液本身所具有的高刚度则大大减少,导致执行器动作失误,自动控制失灵,工作机构产生爬行,破坏了工作稳定性,严重地危害着系统的工作可靠性,甚至还会发生机械事故及危害人身的安全。
2.4 导致气蚀的产生
油液在低压区产生的气泡被带到高压区时,会突然溃灭,气泡又重新凝聚为液体,是局部区域形成真空,周围的油液以很高的速度流向溃灭中心,会对壁面产生较大的局部冲击力,瞬间压力可高达数百甚至上千个大气压,大量的气泡溃灭时会使金属边壁反复受到剧烈冲击而造成疲劳破坏,引起固体壁面的剥蚀,气穴对固体材料表面的这种侵蚀,称为气蚀,它对系统的危害性很大。
2.5 加速液压油的污染
液压油中的气泡或泡沫称为油的无形污染物,它对液压油的危害是相当严重的。它不但可使油液本身的刚度下降、容积效率减小、系统可靠性降底。油中气泡瞬间压缩或破坏时近似于绝热压缩状态,还会使气泡温度急剧升高,引起油温升高(甚至使油液燃烧),导致油中的各种添加剂破坏,产生游离碳、酸质和胶泥状沉淀物,并造成油液发黑,加速了油质的劣化,同时还会使金属产生化学腐蚀作用。除此之外,油温升高还会使油液氧化,使油液的润滑性能下降,加速密封件的老化。
3 防止空气混入液压系统的技术措施
3.1 防止外部气体进入系统,使用中应经常检查油箱量情况是否正常,避免发生吸空现象,同时及时检查油液情况避免油液变质.
3.2 在维修安装中,必须排除元件及管路中空气,并应将吸油管及泵体灌满油液,保持油管的密封良好。
3.3 经常检查过滤器是否堵塞,以免油口压力过低而造成空气分离现象。
3.4 在液压缸和管道上部设置排气装置,用以放掉系统中的空气。
3.5 大惯性的执行器在运动中因突然停止或换向时,会在进油腔形成空穴,为防止形成空穴,应设置补油回路。
3.6 可在油箱吸油侧的底部从中间隔板至箱壁间蒙上一层60――100目的的金属网,把排油箱中油液气体分离出来。
3.7 采用较大直径的吸油管,减少管道局部阻力防止泵产生空穴,同时采用大容量的吸油过滤器防止油液中混入空气。泵的吸油管与系统的回油管口要尽可能的低,两者要尽可能远的距离,并在两者之间加隔板或消泡网。
4 结束语
气泡对液压系统的危害是较大的,应引起高度重视。气泡产生的途径比较复杂,就目前而言,要完全消除和避免气泡对液压系统造成的危害是不可能的,也是不现实的。但是正确认识气泡的危害和产生气泡的主要途径,在液压系统设计中尽可能采取有效的技术手段加以防范,尽量遏制气泡的产生并将其可能造的危害降低到最低程度,是十分必要的,也是完全可能的。此外,除在液压设备设计时采取必要的预防措施在设备运行过程中采取防范措施,消除潜在的故障因素,做到防微杜渐,以保证液压设备安全进行,也是非常重要和不可忽视的。
参考文献:
[1] 雷天觉.液压工程手册[M].北京:机械工业出版社,1990.4
[2] 祁冠方.气泡对液压系统的危害及其对策[J].液压与气动,1995(5)
[3] 汪保明.液压系统的空穴现象及其检测处理[J].液压与气动,1995(5)
篇13:怎样诊断工程机械液压系统的故障论文
1 工程机械液压系统的结构组成。
工程机械液压系统的组成部件主要 10 个部分:①原动机(电动机、发动机):向液压系统提供机械能;②液压泵(齿轮泵、叶片泵、柱塞泵):把原动机所提供的机械能转变成油液的压力能,输出高压油液;③执行器(液压缸、液压马达、摆动马达):把油液的压力能转变成机械能去驱动负载作功,实现往复直线运动、连续转动或摆动;④控制阀(压力控制阀、流量控制阀、方向控制阀):控制从液压泵到执行器的油液的压力、流量和流动方向,从而控制执行器的力、速度和方向;⑤油箱及管路:盛放液压油、向液压泵供应液压油、回收来自执行器的完成了能量传递任务之后的低压油液,管路输送油液;⑥过滤器:滤除油液中的杂质,保持系统正常工作所需的油液清洁度;⑦密封件:在固定连接或运动连接处防止油液泄漏,以保证工作压力的建立;⑧蓄能器:储存高压油液,并在需要时释放之;⑨热交换器(散热器):控制油液温度;⑩液压油:是传递能量的工作介质,也起润滑和冷却作用一个系统中不一定包含以上所有的组成部分,但是液压泵、执行器、控制阀、液压油是必须有的。
篇14:怎样诊断工程机械液压系统的故障论文
(1)故障的复杂性。液压系统出现的故障可能是多种多样的而且在大多数情况下是几个故障同时出现。如系统的压力不稳定,常和振动噪声故障同时出现,而系统压力达不到要求和动作故障联系在一起;机械、电气部分的毛病甚至也会与液压系统的故障交织在一起,使得故障变得复杂,新系统的调试更是如此。
(2)故障的隐蔽性。液压系统是依靠在密封管道内并具有一定压力能的油液来传递动力的,系统的元件内部结构及工作状况不能从外表直接观察。因此,它的故障具有隐蔽性,不如机械传动系统故障那样直观,而又不如电气传动系统那样易于检测。
(3)故障的多样性。液压系统故障中,多种原因引起同一故障,或同一原因引起多种故障,而且这些原因常常是互相交织、互相影响。如系统压力达不到要求,其产生的原因可能是泵引起的,也可能是溢流阀引起的,也可能是两者同时作用的结果。此外,有的粘度是否合适,以及系统的泄露都可能引起压力不足。另一方面,液压系统中往往是同一原因,但因其程度的`不同、系统结构的不同,它与配合的机械结构不同,所引起的故障现象也可以是多种多样的。如同样是混入空气,严重时能使泵吸不进油;轻者会引起流量、压力的波动,同时产生噪声和机械部件运动过程中的爬行。
【油液集中供液系统工程机械论文】相关文章:
2.信息管理系统论文
9.客户管理系统论文
10.客户关系管理系统论文
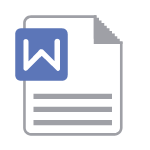





文档为doc格式