抽油机节能电控装置综述
“发呆中”通过精心收集,向本站投稿了9篇抽油机节能电控装置综述,今天小编在这给大家整理后的抽油机节能电控装置综述,我们一起来看看吧!
篇1:抽油机节能电控装置综述1
1 概述
自从100多年前,以燃烧石油制品为动力的机器诞生以来,对石油的需求量飞速增长,也为石油工业的发展提供了契机。随着采油业的发展,产生了被广泛使用的油井举升设备――抽油机。
抽油机的种类繁多,技术发明有数百种。从采油方式上可分为两类,即有杆类采油设备和无杆类采油设备。有杆类采油设备又可分为抽油杆往复运动类(国内外大量使用的游梁式抽油机和无游梁式抽油机)和旋转运动类(如电动潜油螺杆泵);无杆类采油设备也可分为电动潜油离心泵,液压驱动类(如水力活塞泵)和气举采油设备。
目前,应用最为广泛的是游梁式竖井抽油机采油系统,如图1所示。由图1可见,该系统由3部分组成,即地面部分――游梁式抽油机,它由电动机、减速箱和四连杆机构(包括曲柄、连杆和游梁)等组成,详细结构见图2;井下部分――抽油泵(包括吸入阀、泵筒、柱塞和排出阀等),它悬挂在套管中油管的下端,可分为杆式泵和管式泵;联接地面抽油机和井下抽油泵的中间部分――抽油杆柱,它由一种或几种直径的抽油杆和接箍组成。
我国的油田不像中东的油田那样有很强的自喷能力,多为低渗透的低能、低产油田,大部分油田要靠注水压油入井,再用抽油机把油从地层中提升上来。以水换油或者以电换油是我国油田的现实,因而,电费在我国的石油开采成本中占了相当大的比例,所以,石油行业十分重视节约电能。目
前,我国抽油机的保有量在10万台以上,电动机装机总容量在3500MW,每年耗电量逾百亿kW・h。抽油机的运行效率特别低,在我国平均效率为25.96%,而国外平均水平为30.05%,年节能潜力可达几十亿kW・h。除了抽油机之外,油田还有大量的注水泵、输油泵和潜油泵等设备,总耗电量超过油田总用电量的80%,可见,石油行业也是推广“电机系统节能”的重点行业。抽油机节能包括节能型抽油机和抽油机节能电控装置的研制与推广两个方面,对此两大技术的研究方兴未艾。介绍和宣传的文章很多,众说纷纭,莫衷一是。厂家的产品性能介绍亦有“王婆卖瓜”之嫌。因此,有必要将目前常见的几种类型的抽油机节能电控装置作一个科学的分析比较,以供用户选用时参考。在全国各油田进行试验或已投运的节能电控装置不下数十种之多,大体上可以分为5种类型,下面分别加以讨论。
(本网网收集整理)
2 间抽控制器(POC)
由于抽油机是按照油井最大化的抽取量来进行选择的,并且还留有设计余量。另外,随着油井由浅入深的抽取,井中液面逐渐下降,泵的充满度越来越不足,直到最后发生空抽的现象,如果不加以控制,就会白白地浪费大量的电能。对于这种油井,最简单的方法是实行间抽,即当油井出液量不足或发生空抽时,就关闭抽油机,等待井下液量的蓄积,当液面超过一定深度时,再开启抽油机,这样就提高了抽油机的工作效率,避免了大量的电能浪费。
间抽控制的原始做法是派人定时到油井去开停抽油机,即使在发达国家,目前也还有不少油井采用这种人工控制方式,以便解决抽油机的低效和浪费问题。这种做法每天要派人去井场操作好几次,经过长期试验才能摸索出适合各油井的间抽规律,费工费时。于是就引入了定时钟,只须设定开、停机时间,便能自动地进行间抽控制,但是,这仍然无法解决令抽油机的工作能力动态地响应油井负荷的变化,以达到最佳的节能效果,同时,还有可能会影响油井的产量。
为了解决上述问题,通过安装相关的传感器,精确感知油井负荷的动态变化,实现智能间抽控制(IPOC)。为此,可采用各种不同的传感器达到控制目的,下面分别予以介绍。
2.1 液面探测器
如果能直接测出井中的液面,那么就可以用它来控制抽油机的运行。当液面高度超过泵时,就启动抽油机;当液面降到泵的吸入口处时,就关闭抽油机,避免空抽的发生。早期的方法是使用永久式的井下压力传感器来检测液面,现代则是利用声波装置从地面上自动监测井下液面深度,但是,由于装置复杂,维修费用高而没有得到普及。
2.2 流量传感器
在井口通过流量传感器检测油井的出液量,是实现抽油机控制最直接,也是最有效的方法。但是,由于国内的油井产量太低,有些油井的产量每天只有几m3,甚至不足1m3,合10cm3/s。这么小的流量检测,对于各种类型的流量传感器来讲都是一个难题,再加上井中采出的油液中含有大量的泥沙和蜡块,经常会发生堵塞现象,因而也未能获得推广应用。
2.3 电机电流传感器
应当说,电机电流的检测是最方便、最可靠,也是最为廉价的方法。当发生空抽时,下冲程开始
时游动阀并没有打开,光杆载荷为杆柱重量及游动阀上部液柱的重量之和,可平衡掉大部分的配重的重量,电动机只要用很小的能量就可将杆柱送入井底,电机电流较小;当油井中泵的充满度较高时,下冲程开始不久,游动阀即打开,泵中液面托住了游动阀上部的液柱重量,并且使抽油杆柱也浸没在液体中,因而光杆载荷只是杆柱在液体中的浮重,这也就意味着电机将用较大的能量来举起曲柄或游梁尾部的平衡块的重量才能将杆柱送入井底,因而电流就较大。
在下冲程时设置一个设定值,当发生空抽时,实际电流将降至此值以下,控制器就关闭抽油机。也可通过电机的平均电流进行检测,从实际平均电流的下降中也可很容易地鉴别出空抽的发生。但是,电流的检测受到抽油机配重的影响而使实际的电机电流变得很难控制,绝不像某些肤浅的文章中所描述的那样,是近似方波的电流波形。实际的抽油机电动机的扭矩(电流)曲线如图3所示。这种不规则的扭矩(电流)曲线,只有通过抽油机的机械结构和平衡曲线的改变方能改变,而不是通过电控装置可以实现的,因此,这是一个机电一体化的系统工程问题。
2.4 抽油杆载荷传感器
普遍采用的方法是通过特制的传感器,对抽油机的光杆载荷进行检测,因为,光杆载荷是井下泵运行情况的最好监视器,并且它不受平衡配重的影响。泵的充盈系数(包括空抽)通过对抽油杆载荷的分析可以很容易地被检测出来。另外,更重要的是抽油杆载荷数据,加上抽油杆位置的信息,正是分析井下工况的“示功图”的必备数据,利用这些信息可对抽油机的运行情况进行全面的分析。
在光杆或游梁上安装测力传感器可以测出抽油杆的载荷数据。光杆测力传感器比较准确,但易于损坏;安装在游梁上的传感器准确度比较低,但比较耐用。国内已有抽油机专用的测力传感器产品。利用载荷传感器的数据绘制的示功图,检测抽空控制设备的工作原理如图4所示。
抽空控制最可靠的一个方法是计算光杆所做的机械功,因为,机械功与被示功图所封闭的面积成正比,所以,空抽表明输入到系统中的能量减少,只须计算示功图的面积或一部分面积即可检测抽空条件。其方法包括在示功图上设定两条垂直线,计算这两条抽油杆位置线之间示功图的面积或曲线下面的面积,如果用示功图里面的面积,可检测出图4中的面积1减少了;如果用示功图下面的面积,则可检测出面积2增加了。
同时,也可像电机电流信号一样,通过计算光杆载荷平均值的办法来检测抽空的发生,较高的载荷平均值表示有可能发生空抽,而较低的载荷平均值则表示油井中液量多。
总之,间抽控制器的优点和经济效益是显而易见的。
1)由于缩短了抽油时间,大大减少了能量消耗。但是,在用人工控制和定时自动控制间抽时,由于惟恐减产,几乎都会发生实际抽油时间比必要的抽油时间长的情形,因而不能完全避免空抽。通过传感器信号实现闭环控制的智能间抽控制器(IPOC),在检测到空抽时立即关闭抽油机,避免了空抽的发生,平均可多节约能量20%~30%。
2)相对于人工间抽和定时间抽来讲,智能间抽控制由于达到了较低的平均液面,增加了产量。因为,较低的液面意味着较低的井底流压,结果较多的液体流入井底,通常可增产1%~4%。
3)由于消除了液击现象,可使井下和地面设备的维修费用减少25%~30%。另外,通过IPOC装置可提前探测到油井故障,从而进一步减少了所需的修井作业量。
4)使用微电脑技术的IPOC装置大大增加了抽油系统的性能信息检测数据,为抽油机的遥控遥测及集中控制创造了条件。
3 软起动及调压节能型
由于抽油机的功率档次有限,如30kN,60kN,
80kN,100kN等,而每一口油井的参数都不一样,在选配抽油机时,不可能做到量体裁衣,刚好和抽油机的功率档次相匹配,一般留有一定的功率裕量;各型抽油机在配用电动机时,为了保证抽油机在各种工况下正常运行,也留有一定的功率余量;随着油井由浅入深的抽取,油井的产液量越来越少,抽油机的负荷也相应减小。由于上述原因,就造成了抽油机的实际负载率普遍偏低,大部分抽油机的负载率在20%~30%之间,最高也不会超过50%,形成大马拉小车的现象。而当电动机处于轻载运行时,其效率和功率因数都较低,此时若适当调节电动机定子的端电压,使之与电动机的负载率合理匹配,这样就降低了电动机的励磁电流,从而降低电动机的铁耗和从电网吸收的无功功率,可以提高电动机的运行效率和功率因数,达到节能的目的。
3.1 电动机定子绕组△/Y转换降压节能
由于低压电动机在正常工作时,定子三相绕组是△接法,这样每相绕组承受380V的线电压,电动机可产生额定的输出机械功率。电动机的转矩是与电压的平方成正比的,当电动机轻载(负载率<33%)时,可以将电动机的绕组由△接法改成Y接法,使每相绕组只承受220V的电压,即为额定电压的1/,电动机的转矩也就仅为额定转矩的1/3。当负载率>33%时,再将电动机绕组改为△接法运行,否则,会因电流过大而烧毁电动机。电动机在进行Y/△转换时会产生冲击电流。
Y/△接法转换的实现一般采用交流接触器实现,也可以通过晶闸管开关实现,两种方法在节能效果上并无差异,而转换控制电路如何准确掌握转换时的负载率则会对节能效果产生较大的影响。当负载率β<33%时,不能及时进行△→Y切换,则会影响节能效果,而当负载率β>33%时,不能及时进行Y→△切换,则会使电流过大,铜耗增加,反而费电,同样影响节能效果。为了不使转换频繁发生,一般在转换点的负载率之间设置一定的回差,通常采用负载率β<30%时进行△→Y转换,而当β>35%,进行Y→△转换。
3.2 晶闸管相控与调压节电软启动
晶闸管软启动与调压节电的控制框图如图5所示。由单片机控制串联在电动机定子主电路中的晶闸管?触发角α,即可以改变加在定子绕组上的端电压值,从而起到调压节电的目的。其优点是可以动态跟踪电动机的功率因数或输入电功率,达到最佳节能效果;在负载突然增加时也可得到及时的响应,以免电动机堵转;且可兼作电动机的软启动器,同时由于采用单片机控制,具有完善的保护功能。其缺点是造价较高,且由于对晶闸管进行相控,会产生大量的谐波,对电网、电机以及通信系统造成不良的影响,今后这类产品将因达不到电磁兼容的标准而被限制使用。关于电动机降压节电的有关计算和校验,国标GB12497?1995《三相异步电动机经济运行》中有明确的要求。在采取调压节电时,既要达到节电的目的,又要保证电动机轴上的出力,并有一定的过载系数,否则,当负载波动时电动机将发生堵转而烧毁。电动机轻载降压时,首先是功率因数上升,节约了无功功率。这里必须着重指出:不是所有的降压行为都能达到节能的目的,只有当电压的降低程度大于转差率及功率因数的`上升程度时,才能使降压运行的电动机效率得到提高而节能。
经过各种检验计算,电动机降压后的最低电压范围大致为(0.56~0.27)UN。以上数据是以正弦波电压计算的,若考虑到晶闸管调压所产生的谐波,引起电动机的噪音,振动和附加发热等因素,其节能效果还要降低。一台Y1600―10/1730型电动机轻载降压节能效果的计算数据见表1。Y1600―10/1730型电动机的原始数据为:额定功率PN=1600kW,额定电压UN=6.0kV,额定电流IN=185A,额定转速nN=595r/min,最大转矩倍数(最大转矩/额定转矩)=2.22,起动电流倍数(堵转电流/额定电流)=5.53,起动转矩倍数(起动转矩/额定转矩)=0.824,额定效率ηN=94.49%,额定功率因数cos?=0.879。电动机额定负载时的有功损耗ΣPN=93.3kW,电动机的空载损耗Po=29.6kW,空载电流Io=46.25A,电动机带额定负载时的无功功率QN=918kvar,电动机的空载无功功率Qo=480.6kvar。
由表1可知,电动机降压节能,主要节省的是无功功率,提高了功率因数,对供电网有利。而有功节电主要节省的是电动机自身损耗的一部分,且随着负载率的上升而锐减:负载系数β=0.1时,有功节电率为15%;β=0.2时为5.3%;β=0.3时仅为2.1%。按照国标GB12497?1995的规定,综合节电为ΔP+KqΔQ,其中Kq为无功经济当量,其值规定为:电动机直连发电机母线时取0.02~0.04;经二次变压时取0.05~0.07;经三次变压时取0.08~0.1。一般抽油机电动机均经三次以上变压,可取为0.1,也即每节省10kvar的无功功率,可折合为1kW的有功功率计算。由于降压节能时电动机的转速基本上不变,轴上的负载也不变,则电动机的输出轴功率是不会改变的,节省的只是电动机自身损耗的一部分,表1中第7栏综合节电率应为表中第4栏的数据除以当时的负载功率与第5栏的损耗功率之和的结果,并非为节省的综合有功功率与电动机额定功率之比。这是一个概念误区,有些用户在计算节电效益时,往往用电动机的额定功率乘以节电率再乘以运行时间来计算节省的电能(kW・h)数,这是错误的。
表1 按最佳调压系数进行调压后节省的电量计算值
电动机负载系数β 0.1 0.2 0.3 0.4 0.5 0.6 最佳电压调节系统Kum 0.374 0.53 0.647 0.747 0.833 0.916 节省的有功功率ΔP/kW 24.2 17.0 11.0 6.4 3.0 0.86 节省的无功功率ΔQ/kvar 386.5 300.8 224.8 157.0 97.6 47.2 节省的综合有功功率ΔP+KqΔQ 47.4 35.05 24.5 15.8 8.86 3.7 U=UN时电机综合损耗功率∑Pc 59.34 62.04 66.53 72.83 80.93 90.82 损耗节电率/% 79 56.4 36.8 21.7 11 4 综合节电率/% 21.6 9.17 4.48 2.22 1 0.35由表1可知,当负载率为β=0.4时,其综合节电率为2.22%,其节省的功率并非为PN×2.22%=35.52kW,而应当为β=0.4时的负载功率PN×0.4加上电动机当U=UN时的功率损耗ΣPN=72.83kW,来乘以综合节电率2.22%,即(1600×0.4+72.83)×2.22%=15.8kW。有些制造商常在这一问题上误导或欺骗用户,应引起注意。
通过降压对电动机实现软起动的目的,一是减少起动时过大的冲击电流,二是减小全压起动时过大的机械冲击。那么在抽油机上使用降压软起动装置,其效果究竟如何呢?由于电动机的转矩与施加电压的平方成正比,施加电压降低了,电动机的转矩若达不到负载的起动转矩时,电动机是转不起来的。虽然电动机的堵转转矩一般小于额定转矩,但是,当电压降到额定电压的70%时,电动机转矩只有额定转矩的50%,对于起动转矩超过50%额定转矩的负载,是转不起来的。只有当电压升高到电动机的转矩足以克服负载的静转矩时,电动机才能启动。所以,△/Y转换起动只适合起动转矩<1/3额定转矩的负载,一般的软起动也只适合起动转矩<50%额定转矩的负载,对于重载起动的负载就降低起动电流来说,软起动器也是无能为力的。
对需重载起动的负载,使用软起动并不能达到减小起动电流的目的,更不能达到节省起动能量的作用;但是,由于软起动器的电压是呈钭坡上升的,虽然在达到起动转矩前电动机并不旋转,但随着电动机轴上扭矩的不断增大,被拖动的负载是慢慢被加力的,所以,用软起动器起动需重载起动的负载时,可以达到减小机械冲击的目的。对于抽油机来讲,使用软起动器,不一定能达到减小冲击电流的目的,但可以达到减小起动时机械冲击的目的,还是有一定作用的。
在某些宣传降压节能产品的文章中,提到在抽油机处于发电状态时,可以通过调整晶闸管的触发角α改善瞬时过电压的问题,事实上也不尽然。当异步电动机由于负载超速而变成异步发电机运行时,是会产生瞬间过电压,使电动机端电压高于供网电压,但由于供电网可以看成是一个无穷大的电源系统,当稳态运行时,电机端电压只是略高于供网电压,以便能量反馈。这时调整晶闸管的触发角α,只能调整电流,即异步发电机的负荷,对于抑制过电压并无效果。
4 无功就地补偿节能型
交流异步电动机的无功就地补偿就是将补偿电容器组直接与电动机并联运行,电动机启动和运行时所需的无功功率由电容器提供,有功功率则仍由电网提供,因而可以最大限度地减少拖动系统对无功功率的需求,使整个供电线路的容量及能量损耗、导线截面、有色金属消耗量,以及开关设备和变压器的容量都相应减小,而供电质量却得以提高。
无功就地补偿只对长期空载或轻载运行的电动机有用,对于重载运行的电动机,因为其本身功率因数较高,没有补偿的必要。由于抽油机大部分处于轻载运行的状况,且由于其分散性,低压输电线路较长,本身功率因数又偏低,无功就地补偿的效果较好。对于抽油机这样的负载,负载频繁变化,没有必要采用自动投切的电容器组补偿,这样会增加成本,降低可靠性,是得不偿失之举。只要根据电机容量及平均负载率,选配适当容量的电容器进行固定补偿就行了,既经济又实用。目前,由于市售的补偿电容器质量都不好,寿命都不长,因此,应当选用质量较好的自愈式电容器,并有自放电电路的产品。
篇2:抽油机节能电控装置综述2
5超高转差率多速节能电动机拖动装置
5.1作为节能措施的应用
抽油机由于其特殊的运行要求,所匹配的拖动装置必须同时满足三个最大的要求,即最大冲程,最大冲次,最大允许挂重。另外,还须具有足够的堵转转矩,以克服抽油机启动时严重的静态不平衡。因此,往往抽油机在设计时确定的安装容量裕度较大。如6型抽油机配Y200L?6/18.5kW,10型抽油机配Y250M?6/30kW等。20世纪80年代中分别引进国外超高转差电动机(CJT)和超高转差多极电动机(CDJT)技术,对抽油机拖动装置进行了大量的科学实验,测试和分析,证明抽油机匹配CDJT节能拖动装置具有显著的节能效果。
其一,降低抽油机拖动装置的安装容量裕量就是一个节能体现。功率匹配变化见表2。
表2功率匹配变化
抽油机型号
6型
10型
12型
14型
原匹配电动机
Y200L1-6
Y250m-6
Y280M-8
Y315M1-8
电动机
18.5kW
30kW
55kW
75kW
替换电动机
CJT-616kW
CJT-10A22kW
CJT-12A45kW
CJT-1465kW
功率下降率/%
13.5
26.7
18.2
13
电流下降率/%
10
26.3
15
18.8
由表2可知,由于所匹配功率下降,其对应的额定电流相应下降。网络及电机绕组的铜耗与电流平方成正,电流的下降自然带来了损耗的降低而达到节能。
其二,CJT装置软的机械特性造就了抽油机运行过程中电动机功率的有功分量和无功分量的变化,促使输入功率的降低。
分析图6,普通电动机的T=f(s)机械曲线告诉我们,若负载超过Tmax,则电动机不能正常运行,因此,转速在n~n0范围变化较小。而CJT电动机的机械转动曲线告诉我们,T2st>Tst,且速度变化范围大,从0~n0均能运转。
电机机械特性的软、硬就是指转速随转矩变化的大小。“硬”,速度变化小;“软”,速度变化大。
普通电动机的机械特性较硬,在一定负载下,转速n(或角速度ω)较大;CJT电动机机械特性较软,在同一负载下,转速n(或角速度ω)较低,即转差率较大,具有降低扭矩峰值,减小抽油机悬点冲击载荷的作用。因此,在某些工况具有节能效果。
另外,通过对图7所示效率,功率因数与输出轴功率之间的函数关系分析可知:
1)普通电动机的η及cosψ曲线陡峭;
2)CJT电动机的η及cosψ曲线平坦;
3)普通电动机在额定输出功率点,η及cosψ较高,运行最经济;
4)在轻负载时,普通电动机的η及cosψ较低,CJT电动机的η及cosψ较高。
从前面的介绍可知,抽油机固有的设计及运行特点与现场实际运行工况相比,不可避免地出现了大马拉小车的不合理匹配。抽油机维持在PH点的负载,在现场从未出现过,绝大部分负载在电动机额定功率(指输出功率)20%~30%左右。对普通电动机而言,如此运行,其效率和功率因数特低。对CJT电动机来讲,由于曲线平坦,η及cosψ在负载变化情况下,其值变化不大,从而相对来讲其η及cosψ高于普通电动机,致使有功功率降低,功率因数提高。因此,就节能而言,抽油机匹配超高转差电动机是合理的。当然,转差率的高低,机械特性的软硬是否越高越好、越软越好?对于这一问题,我们认为新技术的成立与否是通过生产实践验证的。转差率高低,机械特性软硬均应适度,否则对其实用性、可靠性带来不利影响。
其三,软的机械特性造就了抽油机悬点最大负荷降低,抽油泵上行速度缓慢,抽油杆的弹性变形减小,从而使抽油泵的填充系数增加,吸液量增大,每冲次来油量增加,使单位液耗电能降低。
大量的资料证明,抽油机匹配超高转差电动机,具有显著节能效果,而CDJT变极多速电动机在抽油机应用上其节能效果则更上一层楼。它通过转速的切换而直接导致功率的切换。如6型抽油机原匹配电动机18.5kW,更换为CDJT?5C型变极多速电动机,其功率转换为8/12/16kW三个功率等级,其装机容量分别降低13.5%,35.14%,56.76%,额定电流分别降低15.4%,28%,31.4%。通过功率切换其节能效果非常明显地展现出来。
5.2作为调参(调冲)措施的应用
油田在采油过程中,从工艺或某些特定条件的需要出发,要调整冲次,过去和现在均采用较笨重的办法,由专业人员到现场拆换皮带轮的办法来实现。整个过程需停机进行,执行该任务费事、费时,劳动强度大。采用CDJT变极变速拖动装置,则可由采油工在几秒钟中内非常方便地按下按钮就可实现调冲目的,且不影响生产。特别是有的油田需经常调冲的区域采用该型产品,倍感方便,深受现场生产组织者的欢迎。
5.3降低设备维修费用
CJT抽油机节能拖动装置所具有的软机械性能,改善了抽油机驴头悬点负荷的不均衡性,特别是启动瞬间及启动过程,降低了对抽油机结构件、传动系统的冲击,降低了设备的维修费用,延长了抽油机的使用寿命。
6变频调速节能
当油井的地下渗透能力小于抽油机的泵排量时(绝大多数油井如此),为了提高抽吸效率,降低单位产量的能耗指标,最直接的办法是实行间抽。但是大多数的油井是不允许间歇性工作的,因为如果长时间停机的话,轻则会影响产油量,重则会使油井无法再开启。这是因为:
1)含蜡量高或含盐量高以及油的粘稠度高,且地处高寒地区的油井,如果间歇工作,会造成井口结蜡、结盐或结油的后果,使油井无法再开启;
2)对于注水油井,如果停止抽取,势必会影响产油量,这将是得不偿失的事,对于这类油井,就要采用其它的节能方法。
为了使抽油泵的排量与油井的渗透能力相适应,可以通过改变抽油机的电动机转速来实现。抽油泵是一种柱塞泵,对电动机来讲是一种恒转矩性的负载,也即电动机的电功率与其转速成正比。这里要提醒注意的一点是:有人一说到泵,就想当然地认为和风机、水泵一样属于平方转矩型负载了,或者说“近似于泵类负载”,这都是错误的。要知只有叶片式的风机和水泵,在不计其静扭矩时,有近似于平方转矩的负载特性,也即:排量与转速成正比,压头(或扬程)与转速的平方成正比,而轴功率则与转速的立方成正比。
随着现代电力电子技术的发展,低压变频器已是十分成熟的电气产品,并且其价格也已经大幅度下降,目前进口变频器的价格约为600~700元/kW。国产变频器的价格在400~500元/kW,在抽油机上大量推广变频调速节能改造已经成为可能。抽油机改用变频器拖动以后有以下几个好处:
1)可根据油井的实际供液能力,动态调整抽取速度,一方面达到节能目的,同时还可以增加原油产量;
2)由于实现了真正的软起动,对电动机、变速箱,抽油机都避免了过大的机械冲击,大大延长了设备的使用寿命,减少了停产时间,提高了生产效率;
3)大大提高了功率因数(可由原来的0.25~0.5提高到0.9以上),从而大大减少了供电电流,减轻了电网及变压器的负担,降低了线损,挖掘出大量的“扩容”潜力。
但是,将变频器用于抽油机拖动时,也有几个问题需要解决,主要是冲击电流问题和再生能量的处理问题,下面分别加以分析。
6.1冲击电流问题
如图2(见第3期P183)所示,游梁式抽油机是一种变形的四连杆机构,其整机结构特点像一架天平,一端是抽油载荷,另一端是平衡配重载荷。对于支架来说,如果抽油载荷和平衡载荷形成的扭矩相等或变化一致,那么用很小的动力就可以使抽油机连续不间断地工作。也就是说抽油机的节能技术取决于平衡的好坏。在平衡率为100%时电动机提供的动力仅用于提起1/2液柱重量和克服摩擦力等,平衡率越低,则需要电动机提供的动力越大。因为抽油载荷是每时每刻都在变化的,而平衡配重不可能和抽油载荷作完全一致的变化,才使得游梁式抽油机的节能技术变得十分复杂。因此,可以说游梁式抽油机的节能技术就是平衡技术。
据笔者对某油田18口井的调查,只有1~2口井的配重平衡较好,绝大部分抽油机的配重严重不平衡,其中有10口井的配重偏小,另有6口井配重又偏大,从而造成过大的冲击电流,冲击电流与工作电流之比最大可超过5倍,甚至超过额定电流的3倍!不仅浪费掉大量的电能,而且严重威胁到设备的安全。同时,也给采用变频器调速控制造成很大的困难,一般变频器的容量是按电动机的额定功率来选配的,过大的冲击电流会引起变频器的过载保护,不能正常工作。
通过对抽油机曲柄配重块的调整,可以使冲击电流降到电机额定电流之内,冲击电流与正常工作电流之比在1.5倍以内。这样,选用与电机额定功率同容量的变频器,甚至略小于电机额定功率的变频器(要视抽油机电动机的负载率而定)都可以长期稳定运行。
由于抽油机的起动扭矩往往很大,惯性也很大,所以要将变频器的加减速时间设置得足够长,一般为30~50s,才不致在起动时引起过载保护。
6.2再生能量的处理问题
由于抽油机属位能性负载,尤其当配重不平衡时,在抽油机工作的一个冲程中,会出现电动机处于再生制动工作状态(发电状态),电动机由于位能或惯性,其转速会超过同步速,再生能量通过与变频器逆变桥开关器件(IGBT)并联的续流二极管的整流作用,反馈到直流母线。由于交―直―交变频器的直流母线采用普通二级管整流桥供电,不能向电网回馈电能,所以反馈到直流母线的再生能量只能对滤波电容器充电而使直流母线电压升高,称作“泵升电压”。直流母线电压过高时将会对滤波电容器和功率开关器件构成威胁,为了保护电容器及功率开关器件的安全,所以,变频器都设置了“OUD”保护――直流母线电压高保护停机功能。
1)一种办法是增大变频器直流母线上滤波电容器的容量,将再生能量储存起来,等电动状态时再释放给电动机作功。这种方法对节能有利,但是电容器的储能作用是有限的';譬如,某抽油机电动机的平均功率以10kW计算,回馈功率以25%计算为2.5kW,在一个冲程中发电状态为2~3s的话,则回馈能量Ad=6000J。若采用15kW的变频器,其直流母线滤波电容的容量为2200μF,正常工作时直流母线电压小于600V(Us),“OUD”保护电压(Usm)为800V,那么As=CUsm2-CUs2=×2200×10-6×(640000-360000)=308J,比起6000J的回馈能量来说小得多了。即使再增加10000μF的滤波电容,也只能储能1400J,因此,在大容量或者负载惯量大的系统中,不可能只靠滤波电容器来限制泵升电压。
2)第二种办法是采用“放”的办法,可以采用由分流电阻器Rp和开关管S11组成的泵升电压限制电路,如图8所示。
也就是将回馈能量消耗在电阻上,这是一种耗能的方法,对节能不利。尤其是在大容量或者大惯量拖动系统中,能量的损失较大。
3)对于地处北方寒冷地区的抽油机,为了在冬季增加原油的流动性和防止结蜡,而对井口回油管进行电加热,如采用中频加热装置。这时也可将变频器与中频电加热装置共用整流电路及直流母线,这样可将电动机回馈到直流母线上的再生能量用于中频加热器,同时又防止了直流母线电压的泵升。
4)对于同一井场上有多口油井的场所,可以采用共用直流母线系统方案,即若干台抽油机的变频器可共用一台整流器,将其直流母线联结在一起,利用各变频器的回馈能量不可能在同时发生的原理,将某一台变频器的回馈能量作为其他变频器的动力。这样即节约了能量,又防止了泵升电压的产生。如图9所示。
5)对于更大功率的系统,为了回馈再生能量,提高效率,可以采用能量回馈装置,将再生能量回馈电网,当然这样一来,系统就更复杂,投资也就更高了。所谓的能量回馈装置,其实就是一台有源逆变器。按采用的功率开关器件的不同又可以分为晶闸管(SCR)有源逆变器及绝缘栅双极型晶体管(IGBT)逆变器两种,它们又各有其特点和要求。
――晶闸管有源逆变器
如图10所示,三相桥式可控变流电路用作有源逆变装置,使电网吸收再生电功率。为了使有源逆变电路正常工作,并防止过电流,应满足Um>Ud,其中Ud为变频器正常工作时的直流母线电压,Um为再生直流电压,而Um可通过超前角β(β=π-α)来进行调节。由于
Um=-2.34U2cosβ(或=-1.35U21cosβ)(1)
若有源逆变器交流侧直接接到380V交流电源,且取最小超前角β=π/6,则Ummax为440V左右,而变频器直流母线电压正常工作时在510V左右,则Ud>Um。而我们要求的是,当再生能量较小时,有源逆变装置不工作,让能量储存在滤波电容器中,当直流母线电压达到某一设定值时(如Ud>670V),有源逆变装置才开始工作,将多余的能量回馈电网。根据式(1)反算过去,逆变变压器副边的线电压应大于540V,才能实现电压匹配。
――IGBT有源逆变器
虽然其主电路结构与变频器中的无源逆变器基本相同,但是其功能和控制方法是大不相同的。变频器中的无源逆变器的负载是三相交流电动机,其输出频率、电压、相位都可以由变频器随意控制;而有源逆变器的输出接的是交流电网,其输出频率、相位和电压取决于电网,所以,在IGBT有源逆变器的控制中增加了鉴频、鉴相器和锁相环控制。电压则由PWM控制,比晶闸管有源逆变器容易实现。另外在输出端接有交流电抗器,用来抑制过电流。
6)采用可四象限运行的变频器,如图11所示其控制就更复杂,投资也更高了。
6.3电磁兼容性问题
这里主要讲电磁干扰(EMI)问题,即变频器对微电脑控制器,传感(变送)器及通信设备的干扰问题。变频器是一个很强的电磁骚扰源,变频器中的开关器件,以及SPWM电压波形,会对控制及通信系统造成很大的干扰。干扰的途径,除了感应、辐射之外,还包括传导干扰,即通过连接导线传导的干扰。在控制系统中,变频器只是一个执行机构,它的运行频率(速度)指令由控制器通过对油井液量等信号的控制运算后给予,变频器就通过控制信号线,给微电脑控制器造成了很大的干扰,以致使控制器无法正常工作。因为是传导性干扰,采用屏蔽线是不解决问题的,要从信号线上的共模及差模干扰入手,采用如图12所示的共模与差模滤波器,才能解决干扰问题。
6.4闭环控制的采样
抽油机利用变频器调速,使之动态适应油井负荷的变化,达到节电的目的,必须要加外部传感器,否则无法实现闭环智能控制,只能实现人工定值控制。所采用的传感器的类型,与间抽控制器大体相同,但是在要求上是有差别的。
1)流量检测是最直观、最准确的方法,如果能实现小流量检测并解决防堵问题,应尽量采用流量传感器。
2)光杆载荷传感器也能用来检测井下液量的多少,与间抽控制不同的是,闭环调速控制只要求载荷的变化趋势,不需要标定空抽设定值。光杆的平均载荷大,说明井下液量少,应减速运行,反之则可加速运行。
3)电流控制不可取,因为这里除了配重的影响外,当电机调速时,电流也是随着变化的,因此不能将电流信号用作控制依据。
6.5可靠性和环境适应性问题
由于抽油机都在环境恶劣的野外工作,并且很多油井是无人值守的,所以,对变频器的可靠性和环境适应能力提出了很高的要求。一方面要选用可靠性指标高的变频器品牌,同时也要给变频器在野外恶劣环境下工作创造必要的条件。如设计防护等级高的双层密闭隔垫(保温)控制柜,柜内设计强迫风冷系统,可以将柜内的热量排出,并在柜底设计有冷空气入口,使之适合在夏季沙漠高温环境中使用。如有条件,可建造控制柜小屋,使控制柜避免阳光直接照射及雨淋。
7结语
1)抽油机在油田的使用量大,而负载率普遍偏低,功率因数则更低,电能的无谓浪费严重,节能降耗潜力巨大。
2)间抽控制器在低产油井上节能效果明显,同时因为其投资少,体积小,便于安装,因此推广应用的经济性很好。
3)对于负载率在30%以下的油井,采用Y/Δ转换控制的节能效果明显,且控制简单,投资省,具有推广价值。
4)晶闸管软起动及调压节能,节省的只是电动机自身损耗的一部分,节能效益与其投资不成比例,而其产生的大量谐波,对电网及电机均有影响,因此不宜推广。
5)高转差率多极电机拖动系统,节能效果明显,且能适应油井调参要求,软的机械特性对延长抽油机寿命有利,是很受油田欢迎的电气拖动装置。
6)变频调速系统,使抽油机动态适应油井负荷变化,也可方便地进行调参。配以流量、载荷等传感器,可实现最经济的控制。同时其软起动性能好,对延长抽油机寿命,减少维护费用有利。节能效果最好,能耗基本上与转速成正比,只要降速,肯定节能。是抽油机节能电控装置的发展方向。随着电力电子技术的发展,其价格将进一步降低,而性能将进一步提高。
7)抽油机节能电控装置的发展方向是节能效果好,能与油井负荷相匹配,并有完善的保护功能;有数据采集和存储功能,联网和通信功能,以及遥控遥测功能;并能适应油田的环境要求,操作简单,智能化程度高。(完)
篇3:抽油机节能电控装置综述1
1 概述
自从100多年前,以燃烧石油制品为动力的机器诞生以来,对石油的需求量飞速增长,也为石油工业的发展提供了契机。随着采油业的发展,产生了被广泛使用的油井举升设备――抽油机。
抽油机的种类繁多,技术发明有数百种。从采油方式上可分为两类,即有杆类采油设备和无杆类采油设备。有杆类采油设备又可分为抽油杆往复运动类(国内外大量使用的游梁式抽油机和无游梁式抽油机)和旋转运动类(如电动潜油螺杆泵);无杆类采油设备也可分为电动潜油离心泵,液压驱动类(如水力活塞泵)和气举采油设备。
目前,应用最为广泛的是游梁式竖井抽油机采油系统,如图1所示。由图1可见,该系统由3部分组成,即地面部分――游梁式抽油机,它由电动机、减速箱和四连杆机构(包括曲柄、连杆和游梁)等组成,详细结构见图2;井下部分――抽油泵(包括吸入阀、泵筒、柱塞和排出阀等),它悬挂在套管中油管的下端,可分为杆式泵和管式泵;联接地面抽油机和井下抽油泵的中间部分――抽油杆柱,它由一种或几种直径的抽油杆和接箍组成。
我国的油田不像中东的油田那样有很强的自喷能力,多为低渗透的低能、低产油田,大部分油田要靠注水压油入井,再用抽油机把油从地层中提升上来。以水换油或者以电换油是我国油田的现实,因而,电费在我国的石油开采成本中占了相当大的比例,所以,石油行业十分重视节约电能。目
前,我国抽油机的保有量在10万台以上,电动机装机总容量在3500MW,每年耗电量逾百亿kW・h。抽油机的运行效率特别低,在我国平均效率为25.96%,而国外平均水平为30.05%,年节能潜力可达几十亿kW・h。除了抽油机之外,油田还有大量的注水泵、输油泵和潜油泵等设备,总耗电量超过油田总用电量的80%,可见,石油行业也是推广“电机系统节能”的重点行业。抽油机节能包括节能型抽油机和抽油机节能电控装置的`研制与推广两个方面,对此两大技术的研究方兴未艾。介绍和宣传的文章很多,众说纷纭,莫衷一是。厂家的产品性能介绍亦有“王婆卖瓜”之嫌。因此,有必要将目前常见的几种类型的抽油机节能电控装置作一个科学的分析比较,以供用户选用时参考。在全国各油田进行试验或已投运的节能电控装置不下数十种之多,大体上可以分为5种类型,下面分别加以讨论。
2 间抽控制器(POC)
由于抽油机是按照油井最大化的抽取量来进行选择的,并且还留有设计余量。另外,随着油井由浅入深的抽取,井中液面逐渐下降,泵的充满度越来越不足,直到最后发生空抽的现象,如果不加以控制,就会白白地浪费大量的电能。对于这种油井,最简单的方法是实行间抽,即当油井出液量不足或发生空抽时,就关闭抽油机,等待井下液量的蓄积,当液面超过一定深度时,再开启抽油机,这样就提高了抽油机的工作效率,避免了大量的电能浪费。
间抽控制的原始做法是派人定时到油井去开停抽油机,即使在发达国家,目前也还有不少油井采用这种人工控制方式,以便解决抽油机的低效和浪费问题。这种做法每天要派人去井场操作好几次,经过长期试验才能摸索出适合各油井的间抽规律,费工费时。于是就引入了定时钟,只须设定开、停机时间,便能自动地进行间抽控制,但是,这仍然无法解决令抽油机的工作能力动态地响应油井负荷的变化,以达到最佳的节能效果,同时,还有可能会影响油井的产量。
[1] [2] [3] [4] [5] [6]
篇4:抽油机节能电控装置综述2
5 超高转差率多速节能电动机拖动装置
5.1 作为节能措施的应用
抽油机由于其特殊的运行要求,所匹配的拖动装置必须同时满足三个最大的要求,即最大冲程,最大冲次,最大允许挂重。另外,还须具有足够的堵转转矩,以克服抽油机启动时严重的静态不平衡。因此,往往抽油机在设计时确定的安装容量裕度较大。如6型抽油机配Y200L?6/18.5kW,10型抽油机配Y250M?6/30kW等。20世纪80年代中分别引进国外超高转差电动机(CJT)和超高转差多极电动机(CDJT)技术,对抽油机拖动装置进行了大量的科学实验,测试和分析,证明抽油机匹配CDJT节能拖动装置具有显著的节能效果。
其一,降低抽油机拖动装置的安装容量裕量就是一个节能体现。功率匹配变化见表2。
表2 功率匹配变化
抽油机型号
6型
10型
12型
14型
原匹配电动机
Y200L1-6
Y250m-6
Y280M-8
Y315M1-8
电动机
18.5kW
30kW
55kW
75kW
替换电动机
[1] [2] [3] [4] [5] [6]
篇5:尿素装置节能技术改造小结
尿素装置节能技术改造小结
0 前言 山东阿斯德化工有限公司共有2套尿素装置,A套40 kt/a尿素装置(以下简称A套)采用水溶液全循环法一版通用设计,B套60 kt/a尿素装置(以下简称B套)采用水溶液全循环法二版通用设计.经过多年不断挖潜和技术改造,2套装置合计生产能力已达到300 kt/a.
作 者:辛向阳 王成刚 张旭 罗学英 作者单位:辛向阳,王成刚,张旭(山东阿斯德化工有限公司,肥城,271600)罗学英(宁波远东化工集团有限公司,315040)
刊 名:小氮肥 英文刊名:XIAO DANFEI 年,卷(期): 38(7) 分类号: 关键词:篇6:车用儿童约束装置综述
车用儿童约束装置综述
交通事故是14岁以下儿童死亡的主要原因之一,儿童约束装置(Child Restraint System,CRS)能有效减少交通事故中儿童的伤亡.笔者对车用CRS进行较全面的概述,介绍CRS的定义、工作原理、分类、影响其安全性能的关键部件、国外相关强制性法规、固定装置、试验描述、国外CAE在CRS研发过程中的应用现状等主要内容,并简要指出未来几年欧洲的CRS研究重点.在此基础上,展望我国CRS的研究重点及发展方向,并对我国的'儿童交通安全、CRS技术及其应用,提出下列建议:加强宣传力度,强化人们对儿童乘员的保护意识;制定强制性法规,保证CRS的使用率;在技术方面,重点加强CRS的CAE分析和动态试验研究,开发出适合我国儿童使用的CRS.
作 者:葛如海 苗强 GE Ru-hai MIAO Qiang 作者单位:江苏大学汽车与交通工程学院,镇江,21 刊 名:中国安全科学学报 ISTIC PKU英文刊名:CHINA SAFETY SCIENCE JOURNAL 年,卷(期): 16(4) 分类号:X924.4 关键词:汽车 儿童 约束装置 综述篇7:AMT外围电控装置故障检测的分析
AMT外围电控装置故障检测的分析
机械式自动变速器电控系统含有多个电磁阀与多种传感器,它们出现敝障将严重影响自动变速箱的正常功能.针对外围电控器件出现的.故障,提出了故障诊断策略,并通过采用LabVIEW建立的故障诊断模型进行了验证,为机械式自动变速器原理样机的电控故障诊断系统的开发准备理论基础.
作 者:金昊龙 杜志岐 王颖楠 JIN Hao-long DU Zhi-qi WANG Ying-nan 作者单位:中国北方车辆研究所车辆传动重点实验室,北京,100072 刊 名:车辆与动力技术 英文刊名:VEHICLE & POWER TECHNOLOGY 年,卷(期): “”(1) 分类号:U463.212 TP274+.2 TP277 关键词:AMT 电控装置 传感器 电磁阀 故障检测 LabVIEW篇8:气田甲醇污水处理装置节能技术研究
气田甲醇污水处理装置节能技术研究
甲醇污水处理装置是气田含甲醇污水处理及甲醇回收的核心工艺装置,目前多采用精馏工艺回收甲醇,能耗较大.通过对现有甲醇污水处理装置的综合分析,在大牛地气田第二甲醇污水处理站甲醇污水处理装置的.设计中进行了节能技术研究.采用节能技术的甲醇污水处理装置投产后运行稳定,产品合格,在原料基本相同的情况下,与第一甲醇污水处理站相同处理能力甲醇污水处理装置相比,装置单位能耗降低14 %,节能效果显著.
作 者:单巧利 李勇 王明军 Shan Qiaoli Li Yong Wang Mingjun 作者单位:单巧利,李勇,Shan Qiaoli,Li Yong(西安长庆科技工程有限责任公司,陕西,西安,710021)王明军,Wang Mingjun(中国石油化工股份有限公司华北分公司油建处,河南,郑州,450000)
刊 名:石油化工安全环保技术 英文刊名:PETROCHEMICAL SAFETY AND ENVIRONMENTAL PROTECTION TECHNOLOGY 年,卷(期): 25(6) 分类号:X7 关键词:甲醇污水处理装置 能耗指标 节能技术篇9:电力电子装置谐波问题的综述
关于电力电子装置谐波问题的综述
摘要:随着电力电子技术的发展,谐波的危害已越来越严重,谐波治理问题已经迫在眉睫。对电力电子装置谐波源进行了分析和总结,指出了其危害及相应的谐波管理原则和综合治理方法,并对谐波治理工作进行了展望。关键词:电力电子;谐波;危害;抑制
引言
随着电力电子技术的发展,电力电子装置的广泛应用给电力系统带来了严重的谐波污染。各种电力电子设备在运输、冶金、化工等诸多工业交通领域的广泛应用,使电网中的谐波问题日益严重,许多低功率因数的电力电子装置给电网带来额外负担并影响供电质量,因此,电力电子装置的谐波污染已成为阻碍电力电子技术发展的重大障碍。故抑制谐波污染,提高功率因数的研究已成为电力电子技术中的一个重大课题。本文围绕这一关键问题,通过对电力电子谐波源及其危害的认识和分析,从污染和防治的关系考虑,探讨了综合治理的方法,最后对谐波综合治理的发展趋势进行了展望。
1 电力电子装置――最主要的谐波源
非线性负荷是个谐波源,它引起电网电压畸变,使电压中带有整数倍基波频率的分量。作为最主要的谐波源的电力电子装置主要为各种交直流变流装置(整流器、逆变器、斩波器、变频器)以及双向晶闸管可控开关设备等,另外还有电力系统内部的变流设备,如直流输电的整流阀和逆变阀等。下面对其产生的谐波情况作一分析。
(本网网收集整理)
1.1 整流器
作为直流电源装置,整流器广泛应用于各种场合。图1(a)及图1(b)分别为其单相和三相的典型电路。在整流装置中,交流电源的电流为矩形波,该矩形波为工频基波电流和为工频基波奇数倍的高次谐波电流的合成波形。由傅氏级数求得矩形波中的高次谐波分量In与基波分量I1之比最大为1/n,随着触发控制角α的减小和换相重叠角μ的增大,谐波分量有减小的趋势。
此外,现有研究结果表明:整流器的运行模式对谐波电流的大小也有直接的影响,因此在考虑调整整流电压电流时,最好要进行重叠角、换相压降以及谐波测算,以便确定安全、经济的运行方式;当控制角α接近40°,重叠角μ在8°左右时的情况往往是谐波最严重的状态,所以要经过计算,尽量通过正确选择调压变压器抽头,避开谐波最严重点[1]。
1.2 交流调压器
交流调压器多用于照明调光和感应电动机调速等场合。图2(a)及图2(b)分别为其单相和三相的典型电路。交流调压器产生的谐波次数与整流器基本相同。
1.3 频率变换器
频率变换器是AC/AC变换器的代表设备,当用作电动机的调速装置时,它含有随输出频率变化的边频带,由于频率连续变化,出现的谐波含量比较复杂。
1.4 通用变频器
通用变频器的输入电路通常由二极管全桥整流电路和直流侧电容器所组成,如图3(a)所示,这种电路的输入电流波形随阻抗的不同相差很大。在电源阻抗比较小的情况下,其波形为窄而高的瘦长型波形,如图3(b)实线所示;反之,当电源阻抗比较大时,其波形为矮而宽的扁平型波形,如图3(b)虚线所示。
除了上述典型变流装置会产生大量的谐波以外,家用电器也是不可忽视的谐波源。例如电视机、电池充电器等。虽然它们单个的容量不大,但由于数量很多,因此它们给供电系统注入的谐波分量也不容忽视。
2 谐波的危害
谐波对公用电网的危害主要包括:
1)使公用电网中的元件产生附加的谐波损耗,降低了发电、输变电设备的效率,大量的3次谐波流过中性线时,会引起线路过热甚至发生火灾;
2)影响各种电气设备的正常工作,除了引起附加损耗外,还可使电机产生机械振动、噪声和过电压,使变压器局部严重过热,使电容器、电缆等设备过热、绝缘老化、寿命缩短,以致损坏;
3)会引起公用电网中局部并联谐振和串联谐振,从而使谐波放大,使前述的危害大大增加,甚至引起严重事故;
4)会导致继电保护和自动装置误动作,并使电气测量仪表计量不准确;
5)会对邻近的通信系统产生干扰,轻者产生噪声,降低通信质量,重者导致信息丢失,使通信系统无法正常工作。
3 谐波的管理原则
要提高电能质量,必须加强对谐波的管理。本着限制谐波源向公用电网注入谐波电流,将谐波电压限制在允许范围内的原则。首先要掌握系统中的谐波源及其分布,限制其谐波在允许范围内方可入网,未达标的必须采取治理措施,以防谐波扩散。为此国际电工委员会(IEC)和美国IEEE都有推荐标准,如IEEE规定的电流谐波极限标准见表1。我国结合电网实际水平并借鉴其他国家标准制定的电压正弦波形畸变率规定见表2。
表1谐波电流极限值(IEEE519-1992规定)
Isc/IL
H<11
11 <17 17 <23 23 <35H >35THD <20 4.0 2.0 1.5 0.6 0.3 5.0 20-50 7.0 3.5 2.5 1.0 0.5 8.0 50-100 10.0 4.5 4.0 1.5 0.7 12.0 100-1000 12.0 5.5 5.0 2.0 1.0 15.0 >1000 15.0 7.0 6.0 2.5 1.4 20.0 表2 电压正弦波形畸变率限值 供电电压/kV 电压正弦波形畸变率限值/% 0.38 5 6或10 4 35 3 110 1.5 4谐波的综合治理 目前,我国电力系统对谐波的管理呈现“先污染,后治理”的被动局面,所以如何综合治理已经成为一个迫在眉睫的研究课题。 关于“综合”的内涵,有人认为用范围广泛、普遍推广来描述;也有人认为用集合的、一体化的来表述更实际;笔者认为综合治理的工作应包含以下两方面: ――加强科学化、法制化管理; ――采取有效技术措施防范和抑制谐波。 4.1 加强科学化、法制化管理 主要从两个方面加强管理: ――普遍采用具有法律约束和经济约束的`手段,改变先污染后治理的被动局面,即应该严格按照各类电力设备、电力电子设备的技术规范中规定的谐波含量指标,对其进行评定,如果超过国家规定的指标,不得出厂和投入电力系统使用; ――供电部门应从全局出发,全面规划,采取有力措施加强技术监督与管理,一方面审核尚待投入负荷的谐波水平,另一方面对已投运的谐波源负载,要求用户加装滤波装置。 4.2 采取有效的技术措施 目前解决电力电子设备谐波污染的主要技术途径有两条: ――主动型谐波抑制方案即对电力电子装置本身进行改进,使其不产生谐波,或根据需要对其功率因数进行控制; ――被动型谐波抑制方案即谐波负载本身不加改变,而是在电力系统或谐波负载的交流侧加装无源滤波器(PF)、有源滤波器(APF)或者混合滤波器(HAPF)等装置,通过外加设备对电网实施谐波补偿。 4.2.1 主动型谐波抑制方案 主要是从变流装置本身出发,通过变流装置的结构设计和增加辅助控制策略来减少或消除谐波,目前采用的技术主要有一下几个方面。 ――多脉波变流技术大功率电力电子装置常将原来6脉波的变流器设计成12脉波或24脉波变流器以减少交流侧的谐波电流含量。理论上讲,脉波越多,对谐波的抑制效果愈好,但是脉波数越多整流变压器的结构越复杂,体积越大,变流器的控制和保护变得困难,成本增加。 ――脉宽调制技术脉宽调制技术的基本思想是控制PWM输出波形的各个转换时刻,保证四分之一波形的对称性。根据输出波形的傅立叶级数展开式,使需要消除的谐波幅值为零、基波幅值为给定量,达到消除指定谐波和控制基波幅值的目的,目前采用的PWM技术有最优脉宽调制、改进正弦脉宽调制、Δ调制、跟踪型PWM调制和自适应PWM控制等。 ――多电平变流技术针对各种电力电子变流器(对于电压型的变流器必须用联接电感与交流电源相连),采用移相多重法、顺序控制和非对称控制多重化等方法,将方波电流或电压叠加,使得变流器在网侧产生的电流或电压为接近正弦的阶梯波,且与电源电压保持一定的相位关系。 ――功率因数预调整器在电力电子装置中加入高功率因数预调整器,在预调整器的直流侧通过DC/DC变换控制入端电流,保证电力电子装置从电网中获取的电流为正弦电流并与电网电压同相。此方法控制简单,可同时消除高次谐波和补偿无功电流,使电力电子装置输入端的功率因数接近1。 主动型谐波抑制方案的主要问题在于成本高、效率低。同时,电力电子系统中很高的开关频率使PWM载波信号产生高次谐波,还会导致高电平的传导和辐射干扰。因此在设计主动型谐波抑制方案时,必须用EMI滤波器将高次谐波信号从系统中滤除,防止它们作为传导干扰进入电网;还要利用屏蔽防止它们作为辐射干扰进入自由空间,对空间产生电磁污染。所以对于较大功率的电 力电子装置,一般除了采用主动型谐波抑制方法以外,还要辅以无源或有源滤波器加以抑制高次谐波。 4.2.2 被动型谐波抑制方案 ――无源滤波器(PF)无源滤波器通常采用电力电容器、电抗器和电阻器按功能要求适当组合,在系统中为谐波提供并联低阻通路,起到滤波作用。无源滤波器的优点是投资少、效率高、结构简单、运行可靠及维护方便,因此无源滤波是目前广泛采用的抑制谐波及进行无功补偿的主要手段。无源滤波器的缺点在于其滤波特性是由系统和滤波器的阻抗比所决定,只能消除特定的几次谐波,而对其它次谐波会产生放大作用,在特定情况下可能与系统发生谐振;谐波电流增大时滤波器负担随之加重,可能造成滤波器过载;有效材料消耗多,体积大。 ――有源滤波器(APF)图4为APF原理图,APF通过检测电路检测出电网中的谐波电流,然后控制逆变电路产生相应的补偿电流分量,并注入到电网中,以达到消谐的目的。APF滤波特性不受系统阻抗影响,可消除与系统阻抗发生谐振的危险。与无源滤波器相比,具有高度可控性和快速响应性,不仅能补偿各次谐波,还可抑制电压闪变、补偿无功电流,性价比较为合理。另外,APF具有自适应功能,可自动跟踪补偿变化着的谐波。 APF按与系统连接方式分类,可分为串联型、并联型、混合型和串-并联型。 并联型APF可等效为一受控电流源,主要适用于感性电流源负载的谐波补偿。它能对谐波和无功电流进行动态补偿,并且补偿特性不受电网阻抗影响。目前这类APF技术已相当成熟,大多数工业运行的APF多属此类滤波器。 串联型APF可等效为一受控电压源,主要用于消除带电容滤波的二极管整流电路等电压型谐波源负载对系统的影响,以及系统侧电压谐波与电压波动对敏感负载的影响。由于此类APF中流过的电流为非线性负载电流,因此损耗较大;此外串联APF的投切、故障后的退出等各种保护也较并联APF复杂,所以目前单独使用此类APF的案例较少,国内外的研究多集中在其与LC无源滤波器构成的混合型APF上[2]。 混合型APF就是将常规APF上承受的基波电压移去,使有源装置只承受谐波电压,从而可显著降低有源装置的容量,达到降低成本、提高效率的目的。其中LC滤波器用来消除高次谐波,APF用来补偿低次谐波分量。 串-并联型APF又称为电能质量调节器(UPQC)[3],它具有串、并联APF的功能,可解决配电系统发生的绝大多数电能质量问题,性价比较高。虽然目前还处于试验阶段,但从长远的角度看,它将是一种很有发展前途的有源滤波装置。 有源滤波技术作为改善供电质量的一项关键技术,在日本、美国、德国等工业发达国家已得到了高度重视和日益广泛的应用。但是有源滤波器还有一些需要进一步解决的问题,诸如提高补偿容量、降低成本和损耗、进一步改善补偿性能、提高装置的可靠性等。同时APF的故障还容易引发系统故障,因此各国对此技术还保持着一定的谨慎态度[4]。 ――有源电路调节器(APLC)图5为有源线路调节器(APLC)的原理图,其结构与APF相似,因此过去很多文献上都将其等同于APF。其实,从原理上分析,与APF单节点谐波抑制相比较,APLC是向网络中某个(几个)优选节点注入补偿电流,通过补偿电流在网络中一定范围内的流动,实现该范围内所有节点谐波电压的综合抑制。即通过单节点单装置的装设,达到多节点谐波电压综合治理的功能,APLC的出现,表明电力系统谐波治理正朝着动态、智能、经济效益好的方向发展。 5 谐波综合治理的展望 日益严重的谐波污染已引起各方面的高度重视。随着对谐波产生的机理、谐波现象的进一步认识,将会找到更加有效的方法抑制和消除谐波,同时也有助于制定更加合理的谐波管理标准。加大对谐波研究的投入将会大大加快对谐波问题的解决,当然谐波问题的最终解决将取决于相关技术的发展,特别是电力电子技术的发展。随着国民经济、谐波抑制技术的进一步发展、法制的进一步完善和对高效利用能源要求的增强,谐波治理问题最终将会得到妥善的解决。 随着电子计算机和电力半导体器件的发展,有源电力滤波器的性能会越来越好,价格会越来越低。而用于无源滤波的电容和电抗器的价格却呈增长的趋势。因此有源电力滤波器将是今后谐波抑制装置的主要发展方向。另外,电力电子技术中的有源功率因数校正技术也是极具生命力的。 6 结语 谐波的综合治理工作势在必行。消除电力电子装置谐波污染的工作,可称之为电力电子技术应用的“绿色工程”。电力电子技术的发展必须和这个工程同步,这样才能为高效、低污染地利用电能开辟重要途径,促进我们国民经济的发展和用电设备的革新。同时,电力电子技术的推广和利用才能有更为广阔的发展前景。 【抽油机节能电控装置综述】相关文章: 2.综述范文 3.综述论文格式 4.论文综述 5.楼房节水装置作文 7.节能标语 8.节能口号 9.节能工作总结 10.节能措施
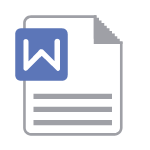





文档为doc格式