研制新一代武器装备的关键-超精密加工
“satsuki”通过精心收集,向本站投稿了10篇研制新一代武器装备的关键-超精密加工,下面是小编给大家整理后的研制新一代武器装备的关键-超精密加工,欢迎大家借鉴与参考,希望对大家有所帮助。
篇1:研制新一代武器装备的关键-超精密加工
研制新一代武器装备的关键-超精密加工
超精密加工技术及微系统制造技术是新一代航空飞行器及其它武器装备发展的关键技术,根据新型机载设备精密、轻量、微型、综合以及多样化的发展特征,开展适应于多种材料(例如特殊光学材料、红外材料、超高强度材料等)、多种产品(例如精密偶件、导引头、导航制导精密零部件、微光学元部件、微传感器等)的超精密加工技术研究以及基于切削加工/特种加工工艺的'非硅类材料的微结构、微系统精密超精密制造与测量技术的研究成为研制新一代武器装备的关键.
作 者:王志标 作者单位:北京航空精密机械研究所 刊 名:航空精密制造技术 ISTIC英文刊名:AVIATION PRECISION MANUFACTURING TECHNOLOGY 年,卷(期): 42(5) 分类号: 关键词:篇2:精密和超精密加工技术的发展
精密和超精密加工技术的发展
精密和超精密加工技术的.发展,直接影响到一个国家尖端技术和国防工业的发展,故世界各国对此都极为重视,投入很大力量进行研究开发,同时实行技术保密,控制关键加工技术及设备出口.随着航空航天、高精密仪器仪表、惯导平台、光学和激光等技术的迅速发展和多领域的广泛应用,对各种高精度复杂零件、光学零件、高精度平面、曲面和复杂形状的加工需求日益迫切.
作 者:王大伟 崔宇 杨坤 陈喜龙 作者单位:装甲兵技术学院,吉林长春,130117 刊 名:科技资讯 英文刊名:SCIENCE & TECHNOLOGY INFORMATION 年,卷(期): “”(14) 分类号:V261.99 关键词:精密 超精密篇3:武器装备研制跟踪的几点思考
武器装备研制跟踪的几点思考
十七大报告指出:全面履行党和人民赋予的新世纪、新阶段军队历史使命,必须把科学发展观作为国防和军队建设的重要指导方针,适应世界军事发展新趋势和我国发展新要求,推进军事理论、军事技术、军事组织、军事管理创新.这些论述为新世纪、新阶段装备建设工作指明了方向.结合现阶段武器装备研制跟踪过程中发现的`一些问题,笔者从军方角度提出几点建议,希望对推进军工产品研制阶段管理工作有所帮助.
作 者:赵大海 李兆龙 杨海琼 作者单位:中国人民解放军第二炮兵驻厂军代表室 刊 名:航天工业管理 英文刊名:AEROSPACE INDUSTRY MANAGEMENT 年,卷(期): “”(4) 分类号:V4 关键词:篇4:非球面模具超精密补偿加工技术
非球面模具超精密补偿加工技术
摘要:为了实现非球面模具的超精密数控加工,研究了加工轨迹算法原理及整个软件系统的结构与实现.提出了基于表面粗糙度均匀化的工件进给速度控制法,分析了工具磨损误差和工件形状误差,重点提出了误差补偿方法,同时也讨论了采用砂轮平行磨削法时避免加工干涉的'方法.软件能生成高精度的加工与补偿加工数控程序文件.最后,在一台镜面磨床上实验加工直径为6 mm的碳化钨透镜模具,经过多次补偿加工后,获得了谷峰值为 0.123 μm, 误差均方根为0.021 μm的表面形状精度. 作者: 尹韶辉 李海峰 陈逢军 王宇 Author: YIN Shao-hui LI Hai-feng CHEN Feng-jun WANG Yu 作者单位: 湖南大学国家高效磨削工程技术研究中心,长沙,410082 期 刊: 纳米技术与精密工程 ISTICEI Journal: NANOTECHNOLOGY AND PRECISION ENGINEERING 年,卷(期): , 08(5) 分类号: HT74 关键词: 超精密加工 平行磨削法 形状误差补偿 非球面光学模具 数控编程软件 机标分类号: TS2 TP2 机标关键词: 面模具 超精密 补偿加工 加工技术 误差补偿方法 精密数控加工 表面粗糙度 形状误差 形状精度 算法原理 软件系统 平行磨削 磨损误差 进给速度 加工轨迹 加工干涉 工件 程序文件 碳化钨 控制法 基金项目: 国家重点科技支撑计划资助项目,国家自然科学基金资助项目 非球面模具超精密补偿加工技术[期刊论文] 纳米技术与精密工程 --2010, 08(5)尹韶辉 李海峰 陈逢军 王宇为了实现非球面模具的超精密数控加工,研究了加工轨迹算法原理及整个软件系统的结构与实现.提出了基于表面粗糙度均匀化的工件进给速度控制法,分析了工具磨损误差和工件形状误差,重点提出了误差补偿方法,同时也讨论了采...篇5:超精密加工设备的发展与展望
超精密加工设备的发展与展望
当今超精密机床技术的.发展趋势是:技术上不断朝着加工的极限方向发展,向更高精度、更高效率方向发展,向大型化、微型化方向发展;功能上向加工检测补偿一体化方向发展;结构上向多功能模块化方向发展;功能部件上向新原理、新方法、新材料应用方面发展,总体来讲是向极限制造技术方面发展.
作 者:杨辉 Yang Hui 作者单位:北京航空精密机械研究所 刊 名:航空制造技术 ISTIC英文刊名:AERONAUTICAL MANUFACTURING TECHNOLOGY 年,卷(期): “”(24) 分类号:V2 关键词:篇6:钛合金精密加工工艺论文
钛合金精密加工工艺论文
1.零件结构特点
TB6钛合金不仅是制造飞机、导弹和火箭等航天器的重要结构材料,而且在惯性导航领域中也逐步开始使用。但由于该材料价格昂贵、难加工以及加工费用高,制约了它的应用。目前我们所承接的导航部件,军方为了提升其强度和寿命,决定淘汰传统的结构钢30CrNi4MoA,使用TB6钛合金材料,这就意味着原来的加工工艺要推倒重来,重新研究TB6钛合金的加工工艺方法。我们对TB6钛合金材料的性能、加工工艺方法及刀具选用等进行了探索和研究,通过各种试验,积累了许多TB6钛合金加工的经验,特别是切削加工用量及刀具的选择,在加工研制过程中得到了验证。本文重点对TB6钛合金精密加工和刀具选用方面的工艺创新作一次全面的阐述,也为今后进一步开展其他钛合金切削加工的研究提供参考与借鉴。TB6钛合金轴向铰轴颈零件如附图所示,其外型复杂,技术要求高,加工难度大。
2.TB6钛合金材料特性分析
钛合金是一种强度高而密度小、机械性能好且韧性和抗蚀性能也很好的不锈钢材料。TB6不锈钢材料加工工艺性差,切削加工困难,特别是在热加工中,非常容易吸收氢、氧、氮和碳等杂质。其加工工艺性主要表现在:(1)摩擦系数大。该材料导热系数低,刀尖切削温度高,切削时产生的切削热都集中在刀尖上,使刀尖温度很高,易使刀尖很快熔化或粘结磨损而变钝。(2)弹性模量小。切削时易产生弹性变形和振动,不仅影响零件的尺寸精度和表面质量,而且还影响刀具的使用寿命。(3)钛合金化学亲和力较强,极易与其他金属亲和结合,在加工中切屑与刀具的粘结现象严重,使刀具的粘结和扩散磨损加大。
3.精加工工艺试验
(1)工艺方法。考虑到该钛合金零件的加工余量比较大,有的部位很薄,只有2~3mm,主要配合表面的尺寸精度、形位公差要求高,在零件的加工工艺方法及工艺流程安排时,按粗加工→半精加工→精加工的顺序分阶段安排加工,同时在每个工序阶段安排热处理工艺,消除加工应力,稳定加工尺寸。这种工艺方法特点主要是通过分阶段的反复加工,减少表面残余应力,防止变形,最后达到设计图样的要求。其主要的加工方法有铣削、车削、磨削、钻削、铰削以及攻螺纹等。
(2)铣削加工及刀具试验方案。钛合金轴向铰轴颈零件加工中,有大量的铣削余量,为了做好铣削加工,我们做了一些试验,特别是在刀具和切削液的选择方面:①刀具材质选择了高硬度、高抗弯强度、韧性和耐磨性好且散热性好的高速W6Mo5Cr4V2Al、W2Mo9Cr4VCo5(M42)和硬质合金YG8、K30、Y330。②铣削时采用水溶性油质切削液来降低刀具和工件的温度,以延长刀具的使用寿命。为了提高铣削加工效率,在加工中心机床上进行了高效铣削试验,结果效率提升了2~3倍,零件表面质量也得到较大的提高。表1、表2所示分别为通过试验总结的切削用量和刀具参数。
(3)孔的精车加工及刀具试验方案。钛合金轴向铰轴颈零件加工中,由于热处理后的表面氧化皮给工艺加工增加了较大困难,为此在加工前用酸洗方法去掉表面薄层氧化皮,然后通过加大走刀量,降低切削速度来车削剩余的氧化皮。在刀具材质的选择、切削用量和切削液的选择方面:①刀具材质选用YG类硬质合金材料。②刀具的几何参数选择前角γ0=4°~8°,后角α0=12°~18°,主偏角j=45°~75°,刃倾角λ=0°,刀尖圆弧半径=0.5~1.5mm。③切削用量按主轴转速n≥230r/min,进给量f≥0.10~0.15mm/r。在同样刀具和切削参数的情况下,选择不同切削液进行切削试验,检查表面粗糙度情况;选定切削液后,使用乳化液冷却,提高了刀具寿度。固定切削参数,选择不同刀具材料进行切削试验,检查表面粗糙度和尺寸控制情况,确定刀具牌号为YG6X、YG10HT;切削液和刀具固定后,选择不同切削参数,对尺寸控制能力进行研究和对目标表面粗糙度实现能力进行验证。
(4)内螺纹加工试验方案。由于内螺纹不便在放大镜下观察,也不便进行尺寸精确测量,选择外螺纹进行替代试车观察表面粗糙度,选好参数后进行内螺纹试车验证,并用粗糙度仪检测验证;选择内螺纹车削加工工艺参数试验,验证上述试验确定的切削液工艺要素和刀具材料要素的适应性,螺纹车削的切削接触刃长,功率需求大,切削参数要进行单独的试验验证。
(5)孔的磨削加工试验方案。磨削加工阶段,由于TB6钛合金的特质,导致了钛合金磨削非常困难,磨削时砂轮磨损严重,轻易会变钝,同时易在表面产生拉应力及烧伤现象。为此在磨削过程中,通过使用切削液和润滑油,使零件充分冷却,保证了精磨质量。磨削砂轮的材料选用绿碳化硅(TL)、黑碳化硅(TH)两种磨料,选择软砂轮R3、ZR1和ZR2,粒度为46、60。磨削用量的`选择如表3所示。
(6)铰削加工试验方案。钛合金的钻削加工也比较困难,常在加工过程中出现烧刀和断钻现象,其主要原因是钻头刃磨不良、排屑不及时、冷却不佳以及工艺系统刚性差等。铰孔是最后一道精加工工序,采用钻孔→扩孔(粗铰)→精铰的加工工艺方法。在刀具和切削液的选择方面:①刀具材料选用M42高速钢或硬质合金K30;刀具的几何参数选择前角γ0=3°~7°,后角α0=12°~18°,主偏角j=5°~18°。校准部分刃带宽度b=0.05~0.15mm,过宽会轻易同钛合金加工表面粘结,过窄会轻易在铰削时产生振动。铰刀齿数为z=4(铰刀直径为12mm)。②铰削时应不断地注入冷却润滑液以获得较好的表面质量,同时应勤排屑,及时清除铰刀刃上的切屑末,铰削时要匀速地进退刀。通过上述几个步骤的试验分析,得出TB6钛合金的各种加工工艺特点,以此为基础,形成TB6钛合金切削工艺方法,并将关键技术点总结出来,拟定了TB6轴向铰轴颈加工的工艺方案。
4.结语
按照我们确定的加工工艺方案进行产品批量加工,达到了轴向铰轴颈的各项精度技术指标,经检测后一次性合格。验证了我们对加工技术难点分析的正确性,说明这种TB6钛合金切削工艺方法是可行的,也积累了经验,开拓了思路。随着科技的高速发展,材料的不断更新,我们需要对新型的惯性导航材料的切削机理、刀具磨损、切削液的选择等状况进行进一步的研究,也需要对切削过程不断进行优化。可以预计,超硬刀具和硬质合金刀具的发展也将在航空、惯性导航等的加工领域中占有很大的一席之地,必将为制造业的发展起到积极的推动作用。
篇7:精密及超精密技术专业简历
精密及超精密技术专业简历模板
精密及超精密技术专业简历模板
张xx
三年以上工作经验|男|29岁(1987年9月16日)
居住地:长沙
电 话:180********(手机)
E-mail:zhangwen@51job.com
最近工作 [ 2年2个月]
公 司:XX公司
行 业:电气系统设计
职 位:PLC编程技术员
最高学历
学 历:本科
专 业:电气工程及其自动化
学 校:上海复旦大学
自我评价
具有扎实的电气自动化专业知识基础,熟知弱电、强电控制理论;已有3年电气编程技术工作经验,了解三菱、西门子、施耐德PLC编程、调试,熟知控制电路设计工作,了解控制元件的选择,电路图的绘制,电路连接指导,现场系统布线设计,现场布线指导,控制系统调试及售后服务等工作;熟悉变频控制系统,会计算机编程,有较好的C+,C++应用编程经验,熟知摸拟电路、数字电路、电子电路的设计;精通AutoCAD、PLC等应用软件操作,也可熟练使用OFFICE系列办公软件;现场工作能力、分析问题的能力强,团队合作意识强。
求职意向
到岗时间:一个月之内
工作性质:全职
希望行业:精密及超精密技术
目标地点:北京
期望月薪:面议/月
目标职能:精密加工工艺师
工作经验
/7—/9:XX公司[2年2个月]
所属行业: 电气系统设计
技术部 PLC编程技术员
1. 根据客户的需求编写项目方案,和客户沟通并开展系统的设计和规划工作,提交相关系统设计和实现文档;
2. 完成电气系统原理图的设计,根据评审通过的设计初稿和客户沟通交流,最终满足客户对电气系统的功能要求;
3. 完成设计实施方案和所需的`测试方案,编制协作配套件的技术文件并提供采购产品的技术资料;
4. 对客户反馈的产品和服务质量进行验证、技术分析与改进完善。
/6—2011 /6:XX公司[1年]
所属行业: 电气系统设计
技术部 编程技术员
1. 独立完成与客户的沟通工作,全面掌握编程技术;
2. 根据给定设计标准、工艺、图纸等独立完成PLC程序和人机界面的编写;
3. 在工程师的指导下完成现场的系统调试,积累较丰富的调试工作经验。
教育经历
/9—2010 /6 上海复旦大学 电气工程及其自动化 本科
证 书
/12 大学英语四级
语言能力
英 语(良好) 听说(良好),读写(良好)
篇8:新一代运载火箭2219铝合金配用焊丝研制
新一代运载火箭2219铝合金配用焊丝研制
针对新一代运载火箭贮箱材料2219铝合金,研制出了适用于常、低温贮箱焊接的焊丝.综合评价结果表明,新研制的焊丝具有良好的制造工艺性能、成分稳定;焊接2219铝合金裂纹敏感性低、气孔敏感性低、焊接工艺性好,接头性能满足指标要求,焊缝组织正常,补焊性能良好,拉伸、冲击均呈韧性断裂特征;接头综合性能优于2A14/BJ-380接头.
作 者:焦好军 胡明臣 周炼刚 常志龙 张志勇 Jiao Haojun Hu Mingchen Zhou Liangang Chang Zhilong Zhang Zhiyong 作者单位:航天材料及工艺研究所,北京,100076 刊 名:宇航材料工艺 ISTIC PKU英文刊名:AEROSPACE MATERIALS & TECHNOLOGY 年,卷(期):2007 37(6) 分类号:V4 关键词:铝合金 焊丝 性能篇9:精密加工技术的现状及发展前景
1 精密加工技术简介
目前,精密加工是指加工精度为1“0.1μm,表面粗糙度为Ra0.1”0.01μm的加工技术,但这个界限是随着加工技术的进步不断变化的,今天的精密加工可能就是明天的一般加工,精密加工所要解决的问题,一是加工精度,包括形位公差、尺寸精度及表面状况,有时有无表面缺陷也是这一问题的核心;二是加工效率,有些加工可以取得较好的加工精度,却难以取得高的加工效率。精密加工应该包括微细加工和超微细加工、光整加工等加工技术。
2 几种常用的精密加工方法及特点
传统的精密加工方法有布轮抛光、砂带磨削、超精细切削、精细磨削、珩磨、研磨、超精研抛技术、磁粒光整等。
砂带磨削 是用粘有磨料的混纺布为磨具对工件进行加工,属于涂附磨具磨削加工的范畴,有生产率高、表面质量好、使用范围广等特点。国外在砂带材料及制作工艺上取得了很大的成就,有了适应于不同场合的砂带系列,生产出通用和专用的砂带磨床,而且自动化程度不断提高(已有全自动和自适应控制的砂带磨床),但国内砂带品种少,质量也有待提高,对机床还处于改造阶段。
精密切削 也称金刚石刀具切削(SPDT),用高精密的机床和单晶金刚石刀具进行切削加工,主要用于铜、铝等不宜磨削加工的软金属的精密加工,如计算机用的磁鼓、磁盘及大功率激光用的金属反光镜等,比一般切削加工精度要高1“2个等级。例如用精密车削加工的液压马达转子柱塞孔圆柱度为0.5”1μm,尺寸精度1“2μm;红外反光镜的表面粗糙度 Ra0.01”0.02μm,还具有较好的光学性质。从成本上 看,用精密切削加工的光学反射镜,与过去用镀铬经磨削加工的产品相比,成本大约是后者的一半或几分之一。
但许多因素对精密切削的效果有影响,所以要达到预期的效果很不容易。同时,金刚石刀具切削较硬的材料时磨损较快,如切削黑色金属时磨损速度比切削铜快104倍,而且加工出的工件的表面粗糙度和 几何形状精度均不理想。
超精密磨削 用精确修整过的砂轮在精密磨床上进行的微量磨削加工,金属的去除量可在亚微米级甚至更小,可以达到很高的尺寸精度、形位精度和很低的表面粗糙度值。尺寸精度0.1“0.3μm,表面粗糙度Ra0.2”0.05μm,效率高。应用范围广泛,从软金属到淬火钢、不锈钢、高速钢等难切削材料,及半导体、玻璃、陶瓷等硬脆非金属材料,几乎所有的材料都可利用磨削进行加工。
但磨削加工后,被加工的表面在磨削力及磨削热的作用下金相组织要发生变化,易产生加工硬化、淬火硬化、热应力层、残余应力层和磨削裂纹等缺陷。
珩磨 用油石砂条组成的珩磨头,在一定压力下沿工件表面往复运动,加工后的表面粗糙度可达Ra0.4“0.1μm,最好可到Ra0.025μm,主要用来 加工铸铁及钢,不宜用来加工硬度小、韧性好的有色金属。
精密研磨与抛光 通过介于工件和工具间的磨料及加工液,工件及研具作相互机械摩擦,使工件达到所要求的尺寸与精度的加工方法。精密研磨与抛光对于金属和非金属工件都可以达到其他加工方法所不能达到的精度和表面粗糙度,被研磨表面的粗糙度Ra≤0.025μm加
1 精密加工技术简介
目前,精密加工是指加工精度为1”0.1μm,表面粗糙度为Ra0.1“0.01μm的加工技术,但这个界限是随着加工技术的进步不断变化的,今天的精密加工可能就是明天的一般加工。精密加工所要解决的问题,一是加工精度,包括形位公差、尺寸精度及表面状况,有时有无表面缺陷也是这一问题的核心;二是加工效率,有些加工可以取得较好的加工精度,却难以取得高的加工效率。精密加工应该包括微细加工和超微细加工、光整加工等加工技术。
2 几种常用的精密加工方法及特点
传统的精密加工方法有布轮抛光、砂带磨削、超精细切削、精细磨削、珩磨、研磨、超精研抛技术、磁粒光整等。
砂带磨削 是用粘有磨料的混纺布为磨具对工件进行加工,属于涂附磨具磨削加工的范畴,有生产率高、表面质量好、使用范围广等特点。国外在砂带材料及制作工艺上取得了很大的成就,有了适应于不同场合的砂带系列,生产出通用和专用的砂带磨床,而且自动化程度不断提高(已有全自动和自适应控制的砂带磨床),但国内砂带品种少,质量也有待提高,对机床还处于改造阶段。
精密切削 也称金刚石刀具切削(SPDT),用高精密的机床和单晶金刚石刀具进行切削加工,主要用于铜、铝等不宜磨削加工的软金属的精密加工,如计算机用的磁鼓、磁盘及大功率激光用的金属反光镜等,比一般切削加工精度要高1”2个等级。例如用精密车削加工的液压马达转子柱塞孔圆柱度为0.5“1μm,尺寸精度1”2μm;红外反光镜的表面粗糙度 Ra0.01“0.02μm,还具有较好的光学性质。从成本上 看,用精密切削加工的光学反射镜,与过去用镀铬经磨削加工的产品相比,成本大约是后者的一半或几分之一。
但许多因素对精密切削的效果有影响,所以要达到预期的效果很不容易。同时,金刚石刀具切削较硬的材料时磨损较快,如切削黑色金属时磨损速度比切削铜快104倍,而且加工出的工件的表面粗糙度和 几何形状精度均不理想。
超精密磨削 用精确修整过的砂轮在精密磨床上进行的微量磨削加工,金属的去除量可在亚微米级甚至更小,可以达到很高的尺寸精度、形位精度和很低的表面粗糙度值。尺寸精度0.1”0.3μm,表面粗糙度Ra0.2“0.05μm,效率高。应用范围广泛,从软金属到淬火钢、不锈钢、高速钢等难切削材料,及半导体、玻璃、陶瓷等硬脆非金属材料,几乎所有的材料都可利用磨削进行加工。
但磨削加工后,被加工的表面在磨削力及磨削热的作用下金相组织要发生变化,易产生加工硬化、淬火硬化、热应力层、残余应力层和磨削裂纹等缺陷。
珩磨 用油石砂条组成的珩磨头,在一定压力下沿工件表面往复运动,加工后的表面粗糙度可达Ra0.4”0.1μm,最好可到Ra0.025μm,主要用来 加工铸铁及钢,不宜用来加工硬度小、韧性好的有色金属。
精密研磨与抛光 通过介于工件和工具间的磨料及加工液,工件及研具作相互机械摩擦,使工件达到所要求的尺寸与精度的加工方法。精密研磨与抛光对于金属和非金属工件都可以达到其他加工方法所不能达到的精度和表面粗糙度,被研磨表面的粗糙度Ra≤0.025μm加
工变质层很小,表面质量高,精密研磨的设备简单,主要用于平面、圆柱面、齿轮齿面及有密封要求的配偶件的加工,也可用于量规、量块、喷油嘴、阀体与阀芯的光整加工。但精密研磨的效率较低,如干研速度一般为10“30m/min,湿研速度为20”120m/min。对加工环境要求严格,如有大磨料或异物混入时,将使表面产生很难去除的划伤,
抛光 是利用机械、化学、电化学的方法对工件表面进行的一种微细加工,主要用来降低工件表面粗糙度,常用的方法有:手工或机械抛光、超声波抛光、化学抛光、电化学抛光及电化学机械复合加工等。
手工或机械抛光是用涂有磨膏的抛光器,在一定的压力下,与工件表面做相对运动,以实现对工件表面的光整加工。加工后工件表面粗糙度Ra≤0.05μm,可用于平面、柱面、曲面及模具型腔的抛光加工。手工抛光的加工效果与操作者的熟练程度有关。
超声波抛光是利用工具端面做超声振动,通过磨料悬浮液对硬脆材料进行光整加工,加工精度 0.01“0.02μm,表面粗糙度Ra0.1μm。超声抛光 设备简单,操作、维修方便,工具可用较软的材料制作,而且不需作复杂的运动,主要用来加工硬脆材料,如不导电的非金属材料,当加工导电的硬质金属材料时,生产率较低。
化学抛光是通过硝酸和磷酸等氧化剂,在一定的条件下,使被加工的金属表面氧化,使表面平整化和光泽化。化学抛光设备简单,可以加工各种形状的工件,效率较高,加工的表面粗糙度一般为Ra≤0.2μm,但腐蚀液对人体和设备有损伤,污染环境,需妥善处理。主要用来对不锈钢、铜、铝及其合金的光亮修饰加工。
电化学抛光是利用电化学反应去除切削加工所残留的微观不平度,以提高零件表面光亮度的方法。它比机械抛光具有较高的生产率和小的表面粗糙度:一般可达Ra0.2μm,若原始表面为Ra0.4”0.2μm,则 抛光后可提高到Ra0.1“0.08μm,加工后工件具有较好的物理机械性能,使用寿命长,但电化学抛光只能加工导电的材料。随着电化学加工技术的发展,还产生了多种新型的复合加工方法,例如超精密电解磨削、电化学机械复合光整加工、电化学超精加工等。它们主要以降低工件的表面粗糙度值为目的,加工去除量很小,一般在0.01”0.1mm,对于表面粗糙度达到Ra0.8“1.6μm的外圆,平面、内孔及自由曲面均可一道工序加工到镜面,表面粗糙度Ra0.05μm,甚至更低。电化学机械加工属于一种加工单位极小的精密加工方法,从原理上讲加工精度可以达到原子级,所以加工精度具有大的潜力,但由于左右其加工精度的因素目前还不是很清楚,所以在实际应用中,其加工表现出一定的不稳定性,这在很大程度上限制了它在工业生产中的应用。
3 超精密加工的发展趋势
国外精密加工技术的发展是从上世纪70年代初期开始的,主要集中在美、日、英等国家,上世纪80年代中期取得了举世瞩目的成果,并在1977年日本精密工学会精密机床研究专业委员会对机床的加工精度标准提出补充IT-1和IT-2两个等级。附表是补充后该标准的内容,由此可以看出比原来的IT0级精度提高了许多。附表 日本精密学 会精密机床分会提
出的精加工等级精度
等级零件机床尺寸
精度圆度圆柱度平面度表面
粗糙度主轴
跳动运动
直线度IT22.500.71.251.250.20.71.25IT11.250.30.630.630.070.30.63IT00.750.20.380.380.050.20.38IT- 10.300.120.250.250.030.120.25IT- 20.250.060.130.130.010.060.13 目前精密加工所能达到的加工精度距加工的极限还有相当的距离。国外有人声称已开发了以原子级去除单位的加工方法,但目前还未在实际生产中得到应用。为了促进精密加工技术的发展,应深入研究和探讨下列几个问题。
1. 基于新原理的加工方法 努力开发加工单位极小的精密加工方法,必须在加工机理的本身就使其误差分散在1nm以下的水平。目前加工单位比较小的加工方法主要有弹性破坏加工、化学加工、离子束加工、电子束加工、等离子体加工等。目前的金刚石切削和金刚石砂轮精密磨削从其加工机理上看,其加工单位就很大。
2. 开发精密的机械机构 不论是加工装置还是测量装置,都需要精密的机械机构,包括导轨、进给机构及轴承等,超精密空气静压导轨是目前最好的导轨,其直线度可达(0.1”0.2)μm/250mm,通过补偿技术还可以进一步提高直线度,但是它没有液体静压导轨的刚性大。同时,由于空气静压导轨的气膜厚度只有10μm左右,所以在使用过程中,要注意防尘。另外 ,在导轨的设计中,还可以用多根导轨并联来均化气膜的误差。用高弹性合金、红宝石制造的滚动导轨,系统误差在0.5μm左右,随机误差可能超过0.1μm。
目前超精密加工中所使用的磁悬浮轴承主轴精度低于空气静压轴承主轴,空气静压轴承主轴的回转精度可达0.05μm,国外的可达0.03μm,但这仍 然无法满足纳米加工对主轴的精度要求。要想提高空气静压轴承主轴的回转精度就必须提高轴承的回转精度,而空气静压轴承的回转精度受轴承部件的圆度和供气条件的影响,由于压力膜的作用,轴承的回转精度是轴承部件圆度的1/15“1/20,所以,要得到10nm的回转精度,轴和轴套的圆度要达到0.15”0.20μm,同时为了气体流出的均匀性,对于纳米级的主轴,多采用
3. 开发高精度的测试系统 在目前的超精密加工领域中,对加工精度的测量主要有两种方法;激光检测和光栅检测,而光栅的应用最为广泛。目前光栅的测量精度可达nm级,如北京光电仪研究中心的光栅系统可达0.1μm,俄罗斯的全息光栅系统达10nm,LG100光栅系统的分辨率可达0.1μm,测量范围为100mm。
开发系统误差小、精度高和可靠性高的检测仪器和控制装置的前提是开发高性能的传感器以及伺服从动机构。如果开发出高性能的传感器以及伺服机构及高精度、高速度、和高可靠性的读出装置,就可通过使用计算机进行检测、分析及计算,以提高检测精度。
与超精密加工有关的技术问题还有很多方面,如温度控制技术、振动控制技术、环境控制技术等。比如材料的弹性变形和热变形,就很难使材料的去除加工达到原子级的精度,长100mm 的钢制零件,要控制其热变形在0.01mm 以内,就必须控制温度变化在0.01℃以内,这在加工领域还很难实现。只要在上述的一个方面取得发展或突破,必将导致精密加工技术
的高速发展。4. 开发适用于精密加工并能获得高精度、高表面质量的新型材料 例如最近开发超微粉烧结金属、非结晶金属、超微粉陶瓷、非结晶半导体陶瓷、复合高分子材料等。只要在上述的一个方面取得发展或突破,必将导致精密加工技术的高速发展。
4 总结
精密加工方法在今天显得越来越重要,精密加工技术已成为目前高科技技术领域的基础,提高超精密加工的精度已成为目前迫在眉睫的问题。目前,很多学者正在这方面做着大量的研究和实验,相信不久的将来,超精密加工会取得长足进展。
篇10:机械制造工艺及精密加工技术探讨论文
摘要:随着科技的不断发展,机械制造工艺以及加工技术不断进步,传统的机械制造工艺以及加工技术已经无法满足人民日益增长的物质文化需要。发展现代机械制造工艺及精密加工技术至关重要,有利于促进机械制造业的发展,提高机械制造以及精密加工的水准。
关键词:机械制造工艺;精密加工;技术
现代机械制造工艺及精密加工技术的发展具有重要作用,不仅能够提高机械制造业以及加工技术的发展水平,还能够促进机械制造业以及精密加工技术的革新,提升机械建造业的综合实力。
【研制新一代武器装备的关键-超精密加工】相关文章:
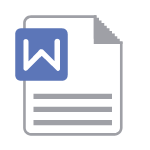





文档为doc格式